A logistics company is an entity that designs, controls, and manages another company’s supply chain. The logistics company can operate during supply procurement, storage, transportation, order fulfilment and distribution, depending on the commercial agreement between the two involved parties.
Logistics entails a wide range of responsibilities and functions. Following are the key functions of a logistics company.
1. Order Processing
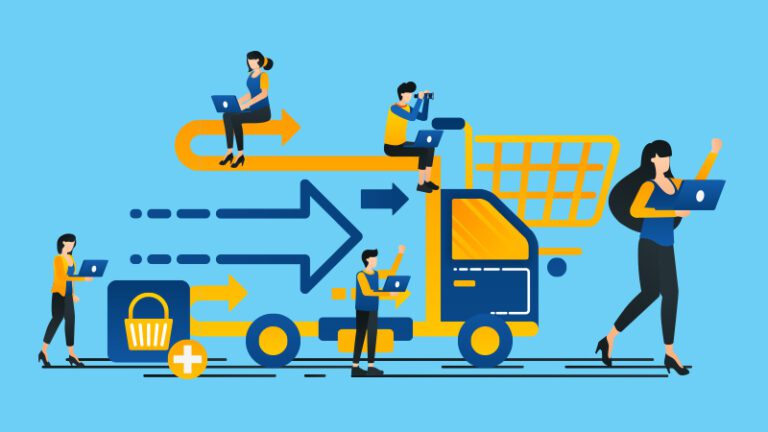
Order Processing is an essential task for a logistics company. The logistics activities begin with order processing, which may be the responsibility of the logistic company’s commercial department. The commercial department ensures that the payment and delivery terms are met before processing the order within the company.
A logistics company follows the following steps for order processing activity:
- Checking the order for any deviations from agreed-upon or negotiated terms
- Prices, payment methods, and delivery schedules are all available.
- Inquiring about the availability of materials in stock.
- Production and material planning in the event of a shortage.
- Recognizing the order, indicating any deviations.
2. Materials Handling
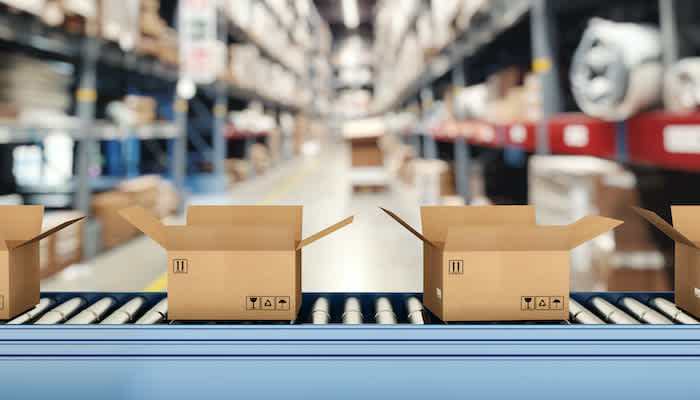
This is the act of moving goods around the warehouse, known as material handling. It entails managing the inventory in a way that allows the warehouse to fulfil orders quickly and accurately. Even though it appears to be a routine job, it is critical and must be done regularly.
For a small shop which has 100 items in the shop, moving one of them around is simple. However, if this small shop is unsure where the products are kept, the shopkeeper will have to look for the product each time he receives an order. There are 100 products in his inventory, so he’ll have to search through them all to find the one the customer ordered before moving the others. Now, multiply the scenario mentioned above by a factor of a hundred. Large companies’ warehouses can be up to half a mile in length. Consider how much inventory there is in the warehouse. If the warehouse manager doesn’t know where the materials are kept and how to be transported to the warehouse’s dispatch centre, he will be in big trouble. His productivity and efficiency will suffer greatly. As a result, the materials handling function is critical.
3. Warehousing
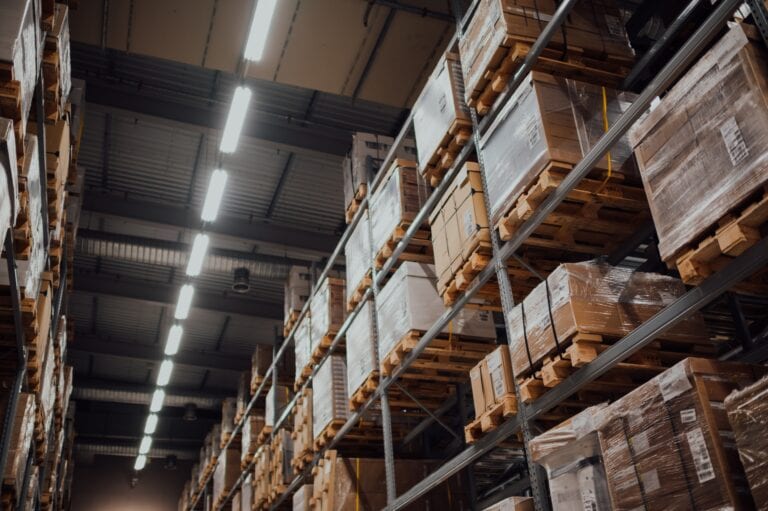
If we take LG or Samsung as an example, these are durable consumer companies with a global presence. While their products may be located in one location, their distribution is global. As a result, warehousing has a significant impact and is an essential Logistics activity.
It is important to note that the warehouse must be close to the retailer or distributor to deliver goods quickly. If a branded product takes a week to deliver, it may not move as much in the market as a competing unbranded product that takes only two days to deliver. As a result, it makes sense for the branded company to establish a more convenient warehouse to provide the products quickly. A brand’s first move in a new territory is to lease a new warehouse, allowing it to be closer to the region and the end customers.
This is a common practice. Logistics centres are strategically placed so that the main warehouse (large warehouses that stock most products) isn’t overburdened. These warehouses can take the pressure off deliveries and become interdependent to ensure that goods are delivered to customers when demand is high, or production is low.
4. Inventory Management
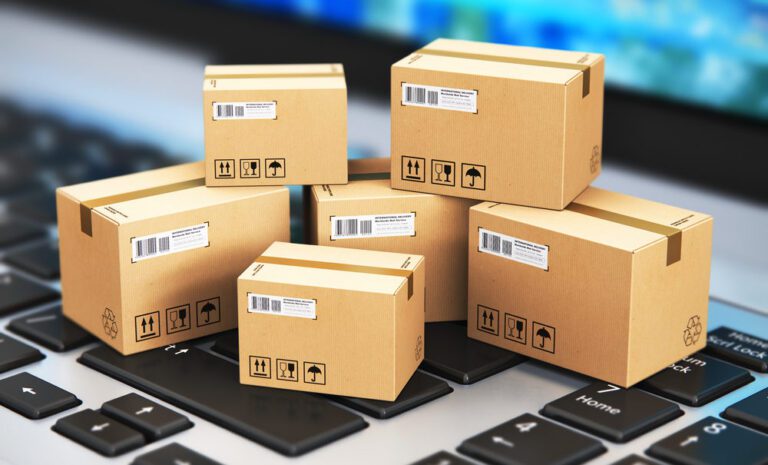
Inventory management is one of the most critical functions of a logistics company. Inventory management is all about maintaining sufficient inventories to meet client demands while keeping the carrying cost to a minimum. It’s essentially a balancing act between providing excellent customer service while avoiding losing market share and the cost of doing so.
If a company has 100 units on hand, but only 10 units are needed to meet demand, it has wasted its money by purchasing 90 of the products. A different company ordered 500 units, but they only produced 200 units because they assumed demand would be lower. As a result, they’ve now lost sales and incurred a loss of opportunity.
Logistics companies use inventory management software which is required to carry out efficient inventory management. It is now possible to solve routine issues such as determining the number of items remaining in a warehouse without conducting a physical inspection thanks to this type of software. It will be necessary to record each inventory operation to optimize the time and precision of the inventory operations, thereby increasing space, optimization and reducing costs.
5. Transportation
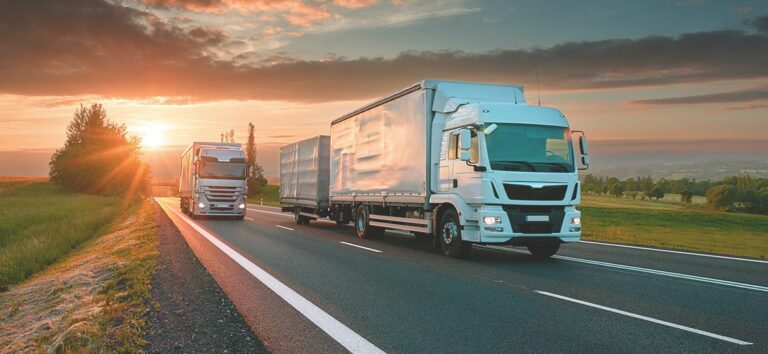
Transportation is one of the most critical activities performed by the logistics company, which is also one of the most resource-intensive and revenue-generating logistics segments. Transportation is expensive for a single reason – Fuel. Whether it’s gasoline, diesel, or natural gas, fuel is a costly resource primarily used in transportation. It is the responsibility of the logistics company to procure LTL or FTL as required for the order shipment.
This is the reason why companies spend tens of thousands of dollars each year to keep transportation costs under control, as it is a significant source of variability for any business. Physical delivery of products from the manufacturer to the distributor or dealer, and then from the dealer to the final customer, is included in transportation.
6. Packaging
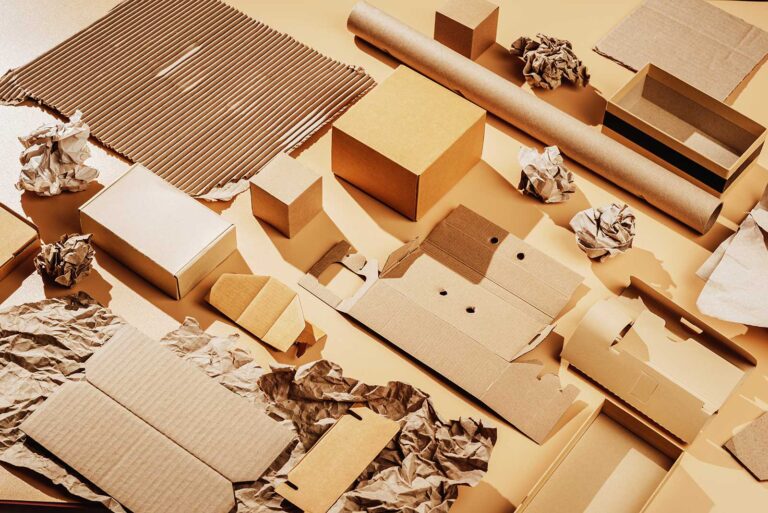
In supermarkets and hypermarkets, the packaging is of two types: one that customers see on a shelf and get attracted to because it seems appealing and prompts the customer to purchase the packages. The second is transport packaging, wherein the products are packed in bulk to prevent breakage or spillage while still allowing them to safely transfer large volumes of the product from one location to another.
The cost-effective packing of the product is the responsibility of the logistics company. If necessary precautions are not taken, end customers may get damaged goods, resulting in severe losses for both the logistics company and the end client. It’s possible that packaging costs 1-2 percent of the product’s value, but if it’s not done correctly during transport, it will cost the company 100 percent because of the damage and loss it suffers.
7. Monitoring
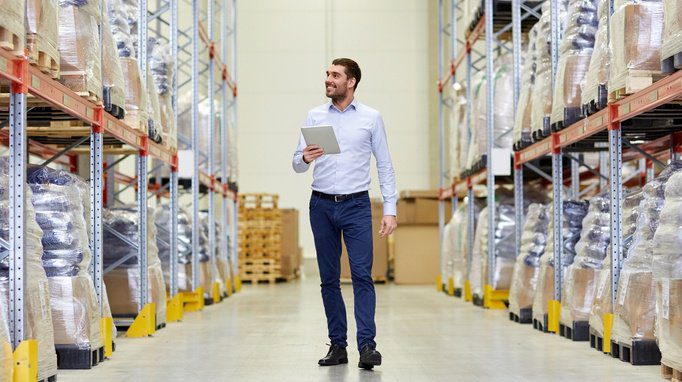
Inventory management, transportation, and warehousing must all be kept up to date by logistics companies. For example, each site requires ongoing information about its current supply status, future commitments, and replenishment capacity.
Similarly, before deciding on a carrier, the logistics company must learn about the availability of various modes of transportation, their costs, and their suitability for services and additional products. It is necessary to monitor and track information on logistics such as space utilization, work schedules, order requests and delivery. Logistics companies help in increasing efficiency by monitoring services and evaluating overall delivery effectiveness.
Conclusion
Logistics is the process of moving goods throughout a company’s supply chain. However, this process consists of various functions that must be managed appropriately to improve the organization’s supply chain’s effectiveness and efficiency.
It is a complex process, but at the end of the day, it all comes down to one thing: the customer experience, which can be easily achieved via reducing costs, improving quality, and accelerating delivery fulfilment. Logistics professionals can drive sales and increase commercial profits through strategic, data-driven planning.
Related posts
- 5 Key Differences Between Supply Chain Management & Logistics
- What Is Reverse Logistics?
- Top 12 Courier Services In Delhi
- Reduce Freight Cost: Best Practices & Strategies
- Reducing Full Truckload (FTL) Costs: 10 Best Practices
- How To Start Logistics Business In India
- 6 Effective Ways To Grow Your Logistics Business
- 4 Major Benefits Of Blockchain In Supply Chain
- Logistics Market In India
- B2B Logistics: Challenges & Opportunities
- Decoding the PLI Scheme for the Indian Manufacturing Sector
- 7 Proven Ways To Improve Your Supply Chain Management (SCM)
- 7 Key Objectives Of Supply Chain Management (SCM)