As the world emerges from the 2020 COVID-19 pandemic, nearly every business is facing significant challenges with rapidly rising commodity prices. Prices for almost everything are on an upward trend, forcing many businesses to make the difficult choice to pass increased costs on to their customers or to find internal savings in already lean times.
The Wall Street Journal reports the problem is particularly bad in the food and beverage industry, where “Costs for cardboard packaging, aluminum for beer cans, labels, transportation, and energy are all going up.”
Do you know if your packaging is using optimum material? Maybe you know your packaging material is not performing at optimum levels, but you don’t know where to start fixing it?
If you answered yes to any of these questions, your business could benefit from a packaging audit.
Reduce Packaging Waste
Packaging waste is one of the most common, and costliest, problems facing businesses looking to run leaner. According to the Supply Chain Solutions Center, due to poor product design and lack of political infrastructure, the majority of plastic waste is sent to landfills or disposed of into the environment. 9.2 billion tons of plastic have been produced, of which only 9 percent have been recycled properly.
Not only is that an environmental problem – at a time when many companies are looking to tout sustainability as a competitive advantage – it drives up costs in more ways than you might think.
It drives up labor costs because handling waste on-site means employees are spending time cleaning and removing waste from your facility. It also means increased landfill and dumping fees.
Consumers are increasingly making purchasing decisions with an eye on sustainability and reward companies that can show real commitment to waste reduction and streamlined processes. Companies and retailers will require much closer collaboration with upstream players, packaging converters, and recyclers to successfully deal with these new challenges.
Historically, many companies have focused on “quick wins” like reducing the weight of packaging materials. That is not likely to cut it any longer, with some of the top Fast Moving Consumer Goods (or FMCG) companies moving toward full recyclability, reduction of plastics, and switching to flexible packaging.
So how can you find a competitive advantage when everyone is combating rising prices? Look at your packaging materials and processes. Companies that can reduce their own packaging costs while maintaining the integrity and brand identity of their products in this volatile business climate stand poised to succeed.
Common Packaging Issues
Evaluate how you pack and ship your product to identify these common issues:
Poorly designed materials storage and packaging lines.
Modifying the layout of your warehouse to be more efficient and identifying and eliminating seldom-used packaging materials are just a couple of ways you can cut costs.
Package design.
Changing the design or structure of packaging can reduce the cost of materials and transit.
Long packaging process times.
Increasing the amount of automation on your packaging line can boost productivity and free up your workforce by cutting down on packing time.
Paying for box dimensions rather than product dimensions.
Using large boxes to ship small items wastes money. Try evaluating your average shipment size and ensure you have appropriate packaging to reduce the dimensional volume rate you pay on items.
Stock reduction.
Storage of packaging can use large areas of your warehouse or fulfillment center – space that could be used more productively. Implementing an inventory management system will reduce storage space, associated costs, and administration.
Ineffective packaging materials that allow damage.
Damaged products not only cost you dollars but also hurts your reputation and branding. If regular damage is an issue, it is time to reevaluate both the packaging materials you use and the performance of your preferred carriers.
Transit damage.
The hidden cost of off-the-shelf packaging. Transit damage leads to high costs for replacing items and high return rates.
Inefficient manufacturing models.
Developing a “just-in-time” model for your packaging line can free up warehouse space and limit the amount of seldom-used materials stored in your facility.
Failing to optimize packaging.
Keeping up with emerging packaging trends – like the shift from plastic materials to fiber or increased use of robotics for sorting and packing – can give you an edge over competitors.
Packaging Audit
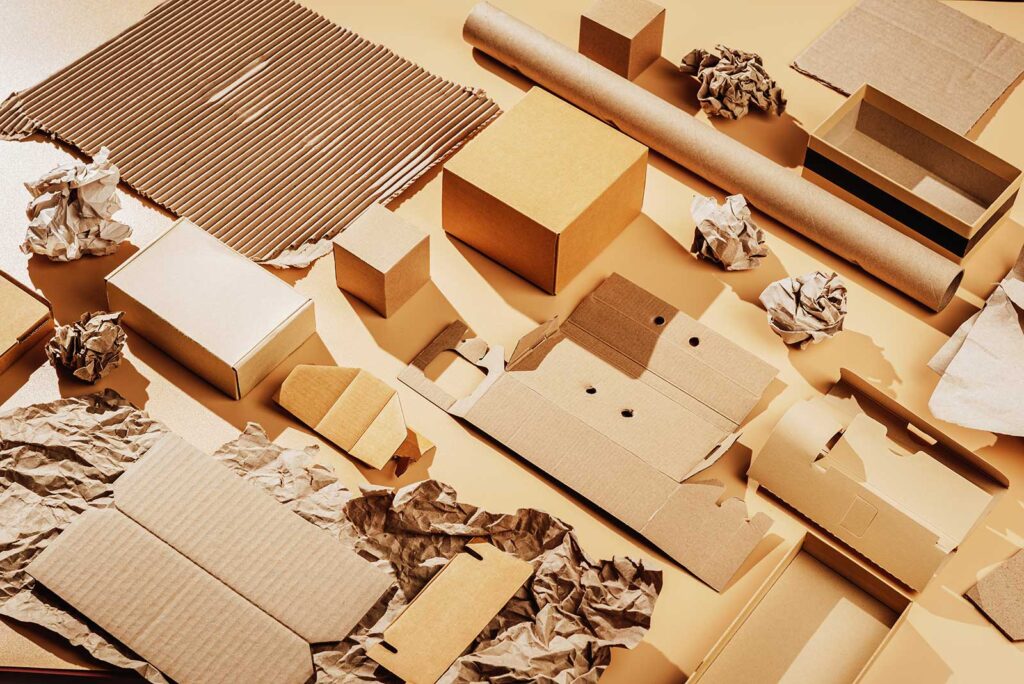
A packaging audit can help you not only identify these opportunities but turn them into strengths. Expert engineers will work with you to make sure you get the most out of your packaging while providing key insights into both your material usage and equipment efficiencies. They can help your team identify potential areas of improvement and provide innovative and practical solutions that will save you money, allowing you to keep your prices down.
In a packing audit, you will receive a complete analysis of each line in your facility followed by recommendations and calibration of equipment, recommended material changes, and training. You can expect to see:
- Reduced unit load costs
- Highlights inefficiencies throughout your packaging processes
- Simplifies supply chain
- Standardized materials across operations
- Minimized downtime
- Increased uptime by reducing unscheduled service
- Usage and cost reduction opportunities directly impacting your business’ profitability
Conclusion
A packaging audit would take a holistic look at your packaging processes, and highlight any opportunities for improving them. Furthermore, a thorough analysis of your usage patterns, overall volumes, and fluctuations in demand, as well as design and material specifications, will allow for opportunities to make your business more profitable.