Supply Chain Management refers to the handling and management of the entire flow of production of a product, starting from product development, sourcing, production, logistics, and final delivery, as well as the information systems required to coordinate these activities.
It is the process of integrating supply and demand management, not only within the organisation but also across all the various channels and members in the supply chain, so they work together most efficiently and effectively.
Supply Chain Management techniques aim to coordinate all parts of the supply chain and minimise total costs with respect to existing conflicts among the chain partners. For example, the retailer wanting to have higher inventory levels to fulfill demand, and on the other hand, the warehouse desiring lower inventories to reduce holding costs may be considered as a conflict.
The organisations that constitute the supply chain are connected through physical movement, involving the transformation, transportation and storage of goods and materials, and information movement, allowing the supply chain partners to coordinate their long-term plans and regulate the day-to-day flow of goods and materials across the supply chain.
Why is Supply Chain Management necessary?
Effective Supply Chain Management systems reduce time, cost, and waste in the production cycle. However, poor SCM can lead to delays, quality issues, and tarnished reputation. In some cases, it can also cause legal problems if suppliers or processes are not compliant. Developments in technology have unlocked enormous potential for Supply Chain Management, facilitating supply chain managers to work closely and in real-time with members of the supply chain.
The objectives of Supply Chain Management include-
- Anticipating Problems: Through careful data analysis, manufacturers can ascertain the demand as accurately as possible and anticipate the shortage before the buyer is disappointed. Other problems that may arise during various stages of the business processes may also be better dealt with proper Supply Chain Management.
- Improving Inventory and Fulfilment: Analytical software helps dynamically allot resources and schedule work based on the sales estimate, inventory count, actual orders and promised delivery of raw materials. This introduces a lot of clarity regarding order fulfilment.
- Adjusting Prices Dynamically: Businesses with perishable products typically adjust prices dynamically to match demand and avoid wastage or shortage. By using analytical software, similar forecasting techniques can improve margins.
Stages in Supply Chain Management
Supply Chain Management can be broadly broken down into the following five steps-
- Planning: It involves outlining the network of manufacturing facilities and warehouses, determining production levels, and drawing up transportation flows between sites. It also comprises devising methods to improve the global supply chain and its management processes.
- Sourcing: It includes selecting suppliers who will provide the raw materials, goods, or services. This involves forming the contracts that govern the suppliers, along with managing and monitoring existing relationships.
- Manufacturing: It is concerned with scheduling of production activities, testing of products, packing and dispatch. Companies should also set rules for performance, data storage, and regulatory compliance.
- Delivering: It generally involves coordinating customer orders, scheduling deliveries, dispatching loads, invoicing customers and receiving payments.
- Returns: It encompasses all product returns, including defective products and products that will no longer be manufactured or sold. This stage also includes components from other stages, like inventory and transportation management.
Benefits of Supply Chain Management
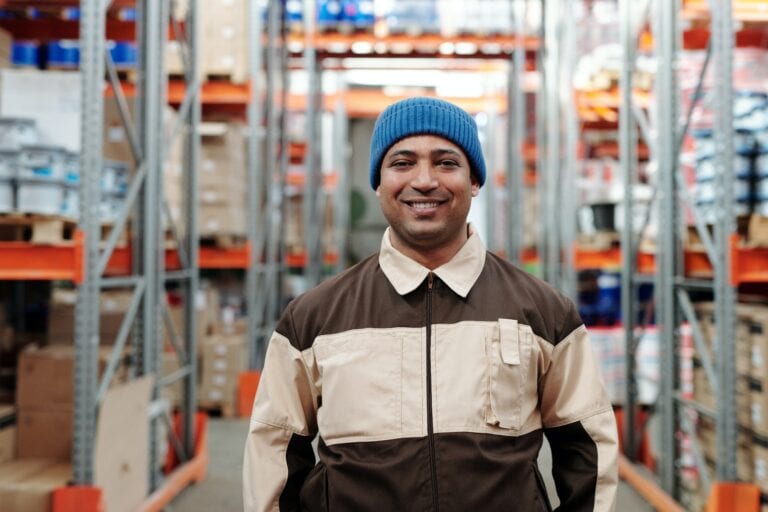
To ensure qualitative progress and survive the competitive environment, a business must invest in efficient Supply Chain Management to effectively and sustainably respond to disruptions. As globalisation makes supply chain processes more complex, businesses are increasingly turning to analytical solutions to enhance their decision-making capacities and improve the efficiency of their supply chains.
Supply chain optimisation offers various benefits that improve the overall functioning of an organisation. A few of the most prominent advantages of effective Supply Chain Management are as follows-
- Better Quality Control: Efficient Supply Chain Management directly affects the quality of a company’s products and services. This compliance contributes to customer gratification and sustainability. Moreover, companies with greater control over their suppliers enjoy improved quality control. Process guidelines can help suppliers comply with the company’s quality requirements. Some companies go beyond simply providing criteria, requesting documentation verifying suppliers’ compliance steps or conducting periodic audits. By analysing performance data, corporations can partner with the highest-performing suppliers and vendors to maintain strict quality control.
- Optimised Shipping: Because of increasing costs, shipping optimisation is a prime concern for supply chain managers. Inefficient shipping techniques cause delays and interruptions in the supply chain and lead to increased costs. Identifying the most suitable shipping methods for large bulk orders, small parcels, and other shipping scenarios helps businesses get orders to customers rapidly while minimising costs. Not only does this boost the company’s net income, but it also improves customer satisfaction.
- Reduced Overhead Costs: Warehouse fulfilment costs contribute massively to overhead. Optimising the warehouse layout, implementing the appropriate automation solutions to improve productivity and adopting a better inventory management system helps reduce these costs. Supply Chain Management includes inventory management, which, when effectively planned and executed, may help cut down costs. In order to maximise internal inventory, Supply Chain Management has inventory management software that allows managers to make use of an on-demand inventory model. Besides, with adequate accounting management and automated processes, businesses can guarantee maximised cost-effectiveness.
- Improved Risk Management: Analysing the big-picture and supply chain data can disclose potential risks, allowing companies to keep backup plans in place to respond to unexpected circumstances promptly. By taking proactive action, companies can avoid negative consequences. Understanding risks also helps companies obtain leaner operations.
- Higher Efficiency: When a company’s supply chain operations, including resource procurement, logistics, and delivery, are tactically planned and executed, businesses can predict demand more precisely and cater to them. This strengthens the efficiency of a company to respond to disruptions, fluctuating industry trends and ever-evolving markets. Furthermore, having real-time data on the availability of raw materials and manufacturing delays enables companies to implement backup plans, like sourcing materials from a backup supplier, avoiding further delays. Without such data, companies usually don’t have time to initiate plan B, resulting in problems such as late shipments to consumers or out-of-stock inventory.
- Better Technology: The hand of digital technologies in improving the functionality of Supply Chain Management is substantial. With comprehensive tools and cutting-edge software in place, businesses can scale their services sustainably and in a cost-efficient manner. From efficiency, performance and risk mitigation to customer experience, technology plays an imperative role in streamlining every phase of the supply chain. For instance, businesses may include cloud-computing, artificial intelligence, machine learning, 3D printing, etc., in their supply chain operations to enhance their existing supply chain.
Measuring performance of SCM
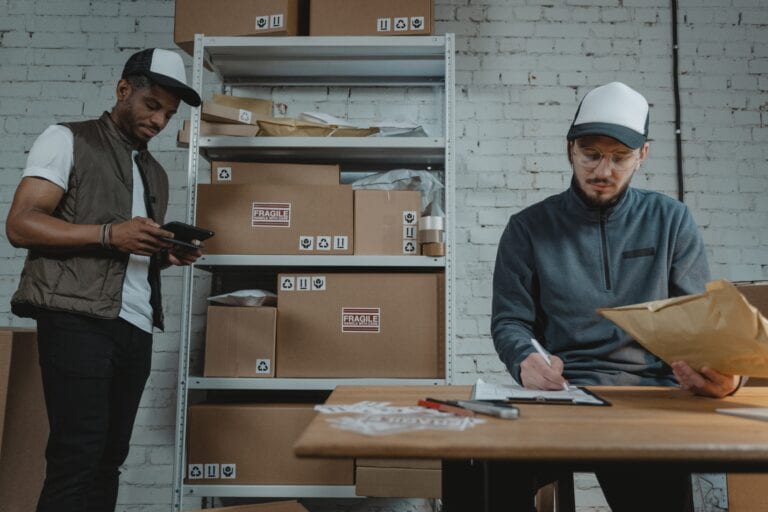
Key Performance Indices (KPIs) help identify desired performance standards and allow supply chain managers to measure performance against those standards and locate areas needing attention and correction. Also, they are useful in measuring performance improvements. Common KPIs include-
- Inventory Turnover: It is an efficiency ratio that determines the number of times inventory is used or sold over a period such as a year, which is another factor affecting working capital.
- Cash-to-cash Cycle Time: It is the number of days between paying for components and raw materials and receiving payment for a product.
- Perfect order rate: It is the number of orders delivered without mistakes, which is a critical metric for e-commerce organisations striving for perfection.
- GMROI: It is an inventory profitability analysis ratio that interprets a firm’s ability to turn inventory into cash over the inventory cost.
The scope of Supply Chain Management goes beyond simply managing suppliers as and when necessary. In fact, it’s about determining suitable supply chain strategies and taking data-driven steps to execute them. Modern supply chains benefit from massive amounts of data produced by the chain process and organised by data scientists and analytical experts. While improper management of the supply chain can cost the business a fortune, efforts made towards maintaining an efficient supply chain provide the much needed competitive edge to the enterprise. Hence, stakeholders are increasingly paying attention to this crucial aspect of their business.
Related posts
- 7 Proven Ways To Improve Your Supply Chain Management (SCM)
- An Ultimate Guide To Inventory Management
- 7 Key Objectives Of Supply Chain Management (SCM)
- Top 10 Ways To Reduce Supply Chain Costs
- 9 Primary Benefits Of Supply Chain Management
- The Ultimate Guide To Supply Chain Risk Management
- Top 7 Supply Chain Risk Management Strategies
- 8 Best Inventory Management Practices
- Logistics Market In India
- 4 Major Benefits Of Blockchain In Supply Chain
- Top 7 Supply Chain Management Challenges
- 5 Key Differences Between Supply Chain Management & Logistics
- How To Achieve Supply Chain Excellence In Manufacturing