The primary structural interface which is used for keeping and handling unit loads is called a pallet. Pallets are a highly essential component of warehousing services. They act as the backbone of the warehousing system. They prevent damage to the product, act as cushions to forces that may cause breakage, and protect the goods in all storage facilities. Their presence ensures that all items reach their destination safely.
History of Pallets
Pallets came into existence in the 20th century. People adopted the system of primarily using these pallets for storage and handling in logistics around the same time. As the pallets developed, they, in turn, helped modernise the system of logistics today. Earlier, loose stacking of goods was performed, which was inefficient and caused severe damages to the products. With the advent of pallet storage, there was a significant impact on the efficiency of transport and shipping of goods. Due to urgent requirements, several additions were made to the design of the pallet during world war two hence improving it manifold. Companies made the following changes at that time-
- Reuse of pallets was started.
- Double stacking was done using pallet collars for fragile materials.
- They introduced the pallet pooling concept.
Types of pallets
a) Based on dimensions
- Europallet: Its measurements are 1200mmx800mm. Primarily used in Europe, the European Pallet Association runs it and claims that about 500 million such pallets are in circulation. The International Organization for Standardisation(ISO) has provided certification to this type of pallet. The measurements are usually decided based on the vehicle that will carry it to cover maximum space. It has its own weight of 25kg and can support a load of 1500kg when it is being moved.
- American Pallet: Its dimensions are 1200mmx1000mm. These are primarily used in American and Japanese supply chains. They are also known as universal pallets or isopallets. They also weigh approximately 25kgs and can carry 1500kg on the move. When kept on a static, solid and smooth surface, not more than 6000kg can be held on the pallet.
- Few other measurements that the ISO has standardised are 1016x1219mm, 1165x1165mm, 1067x1067mm and 1100x1100mm. Their usage is much less than American and Europallet.
b) Based on the number of entry points
Entry points are the points at which the forklift inserts the fork to transport the load from one place to another.
- 4 Entry Points: This means that the pallet is accessible from all its sides, and workers can use a forklift from either one of them for movement.
- 2 Entry Points: The labour can only access them from two opposite sides of the pallet. This means less mobility than the pallet with 4 Entry Points.
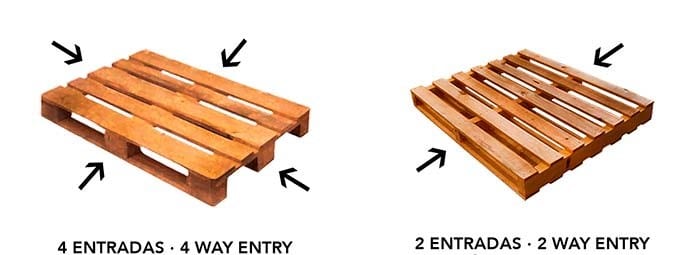
c) Based on Material
- Wooden Pallet: Pallets made of wood are the most widely used ones. They are high in demand and have a market share of about 90-95%. They are highly reliable and have resistance to damage. They are eco-friendly and easy to repair and recycle. This increases the duration of their life cycle. Other than these benefits, wooden pallets’ only drawback is their difficulty in cleaning.
- Plastic-made Pallet: These pallets have a growing edge over wooden pallets. Users can easily clean them, they are lighter in weight, recyclable, and have greater resistance to damage if they are knocked over. However, they tend to get deformed easily and cost extra. Repair is not possible in plastic pallets.
- Metal Pallet: These are generally made of steel or aluminium and are used in the metal industry. They are the heaviest and most durable. They can be cleaned easily. However, their weight increases the cost of shipment.
- Cardboard Pallet: These are primarily used for light loads. They are disposable, recyclable, easy to handle and eco-friendly. They are the cheapest among all subtypes; however, they have a short life span.
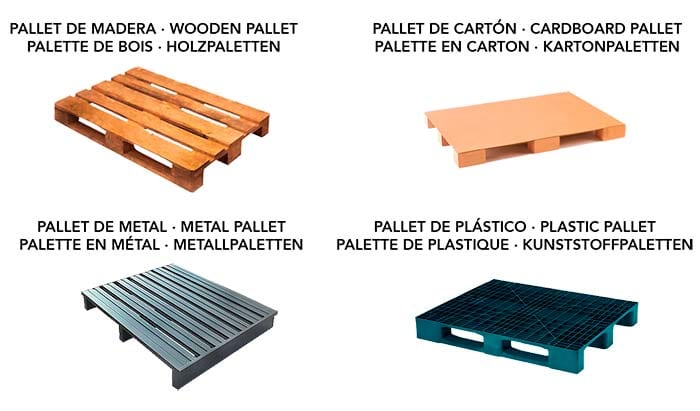
d) Other Types
- Reversible Pallet: Load can be put on these pallets from both upward and downward side since they are identical and homogenous.
- Closed Pallet: They can only be loaded from one side and are “closed” by a slab on one of the backs.
- Wing Pallet: Projections on two to four sides of such wing pallets that help facilitate the use of a fastening system.
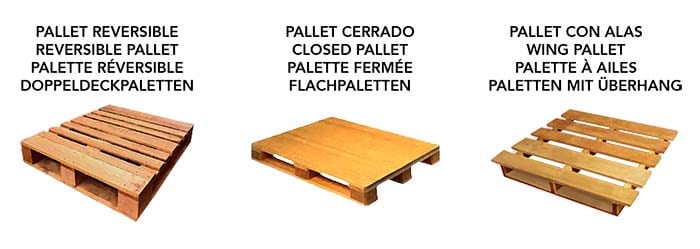
Pallet Storage Methods
- Block Stacking: Pallets with unit loads are stacked one over the other and arranged in lanes on the warehouse floor. Condition of the pallet, weight it is supporting, the capacity of the forklifts determines the height clearance at which various loads are kept.
- Stacking Frames: Decks and posts are used to make the stacking frames. These can be moved from one place to another. These stacking frames are used to store loads that are not stackable. Stacking can be done for a great height using these frames. Companies also use them for temporary racking during busy periods.
- Single-Deep Pallet Rack: This system helps access each pallet individually. Thus, workers can replace each pallet directly at its spot. There can be various configurations of this rack in which each pallet is placed at varying heights. This method is used widely. The only drawback of such a system is its requirement for a large floor area.
- Double-Deep Pallet Rack: It is a variant of the single deep rack system with two pallets stacked together. It helps reduce the requirement for a large number of aisles. A particular double reach forklift is needed to remove pallets from the racking.
- Drive-In Rack: These have spaces for 5-10 pallet loads. It has drive-in lanes which help access the stack with a forklift for placement and removal of pallet loads in piles. Handling loads becomes more accessible due to this. However, as less space is provided, using a forklift becomes a tedious and time-taking process since it becomes difficult to operate.
- Pallet Flow Rack: A conveyor belt is used to remove the items from one end of the stack. This way, the removal takes place such that the item placed first inside the stack can be removed first. Then the next pallet takes its place. However, it proves to be a costly option.
Push Back Rack: A rail-guided carrier is used to push the load into the stack. With every load being put in the stack, all the other loads move further backwards. This way, once a single load is removed, the other moves to its position. Thus, the stock can be removed as required based on its position.
Benefits of Palletisation
Using pallets always give a strategic and competitive edge to warehousing companies over their competitors. Manual storage that needs to be done in the absence of palletisation can lead to several human errors and faults. Therefore, pallets help in reducing the difficulty in handling goods by increasing their efficiency.
The benefits of using pallets are as follows-
- Faster unloading and loading – This helps in better transportation and on-time arrival or dispatch of goods. Delivery vehicles are better organised and easy to manage.
- Decreased Labour Requirement – Since palletisation helps mechanise the process of storage and transportation. Thus, manual handling and its problems are significantly reduced.
- Temperature-sensitive products are better protected – Goods that are perishable and are being stored in warehouses that do not have temperature control run a lesser chance of being spoiled when stored in pallets.
- Lesser risk of damage – Pallets are like protective equipment that keep the goods safe. Since they are appropriately stacked up in storage and transport, they are prevented from falling or being knocked up.
- Workers are safer – Since the engagement of labour is lesser, the possibility of injuries to workers is lesser. This way, goods will not fall on the workers, or irregular edges will not cause abrasive injuries.
- Standardisation – Since, almost all pallets have predetermined sizes prescribed by standard guidelines, stacking of pallets can be precisely planned before dispatch or even during transport.
New Trends in Pallets
Recently, efforts have been made to increase the load-bearing capacity of pallets. Further, an approach to increase the number of stored goods on each pallet has been taken. Technological steps towards allotting automated identification to each pallet have been experimented. Concerns have been raised regarding food storage and perishable goods. Also, the cleaning process for pallets has been questioned several times. Thus, work towards solving this issue has been underway. Information and technological advancement has opened up several options for pallet optimisation. This has been done by creating automatic systems. However, these are expensive due to their requirement for high-quality pallets. Environmental concerns have also raised reusability and recyclability issues. Many pallet companies have also considered pooling their resources, for example, Brambles – CHEP and IFCO; Euro Pool System and LPR. This way, there was scope for increasing complementary offers and free services.
Frequently Asked Questions (FAQs)
Ans. During the holiday season, which are the last 6 months of the year, pallet sales are at its peak time. However, pallets are the cheapest during summer months due to the lower demands.
Ans. Companies can draw an estimate for the number of cartons by dividing the surface area of a pallet by 1.5. This is determined considering palletisation begins at the origin. However, they can only decide a final number after actual palletisation takes place.
Ans. Since plastic pallets are made of one piece, they have higher durability than wooden pallets.
Ans. More than one person should carry a pallet considering its bulky nature. However, if one person is lifting it it must be lifted with the correct posture and stance from the corner. Further, forklifts are used to carry and transport pallets from one place to another inside a warehouse.
Related posts
- Pallets In Logistics: A Comprehensive Guide
- Chennai Warehousing Market Report – 2020
- Warehousing in Delhi/NCR – Report 2021
- Warehousing In Hyderabad : Report 2021
- 6 Major Types of Cold Storage
- 6 Major Advantages of Cold Storage
- Industries And Applications of Cold Storage
- 5 Core Functions Of Third-Party Logistics (3PL) Providers
- What Is Warehousing?
- Going Up: Logistics Leaders Solve Warehouse Space Constraints
- Top 10 Warehousing Companies In Chennai [2025 List]
- Top 10 Warehousing Companies In Kolkata [2025 List]
- Cold Storage: Challenges & Opportunities