Why do we need a resilient supply chain?
A resilient supply chain is categorised by its ability to withstand and recover from setbacks. This means being able to endure, if not completely avoid, the effects of a supply chain disruption. Such disruptions include sudden changes in consumer behaviour, unpredictable political and trade climate, obsoletion of technology, etc.
Companies all over the world are increasingly looking to invest in supply chain technologies and other measures in order to achieve more efficient operations, increased productivity, and risk reduction, among other benefits.
The most robust and flexible supply chains are built with modern technologies that enable businesses to forecast, anticipate, and respond promptly to any threats or opportunities that the future may bring. Hence, business owners and managers are actively realising that building a resilient supply chain is a necessity in today’s competitive market.
Disruptions and shocks are inevitable in today’s dynamic market. What distinguishes a successful business from the rest is its ability to cope with and make the best out of such unforeseen circumstances.
We have further discussed the 6 key steps to build a resilient chain.
1. Efficient Management of People
Companies require qualified personnel with specialised skills to plan and execute the strategies to overcome business obstacles. You should look for competent engineers, procurement specialists, and supply chain managers to help the organisation navigate a challenging business environment. It is also critical to conduct disruption management training for your employees to familiarise them with common business disruptions.
Moreover, you should form a commodity management team as well as a supplier relationship team. Commodity managers are professionals in their respective commodities markets and focus on short-term goals. This means they are continuously looking for new products, supply chain advancements, pricing changes, and other market activity. Such insight can help in mitigating the effects of cost hikes and component shortages.
Supplier relationship managers deal with a long-term technology plan. These professionals are committed to developing executive-level connections with suppliers by knowing their core business strategies and engaging these partners with chances for mutual benefit.
2. Strategic Planning
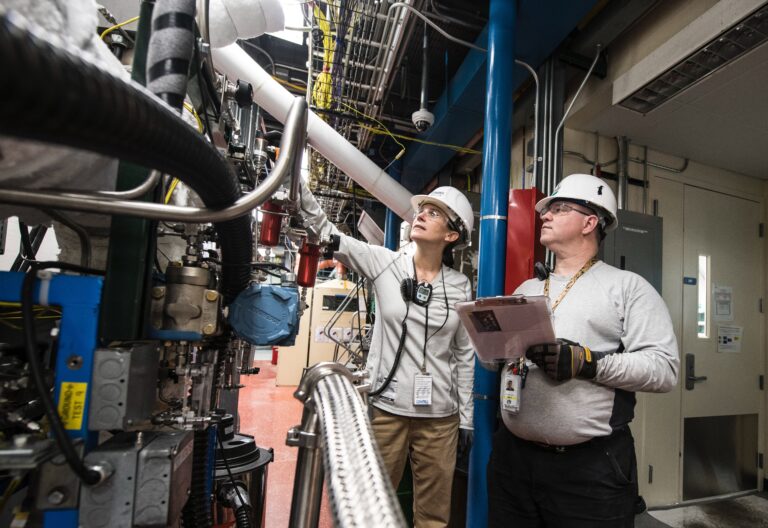
A critical step in achieving supply chain resiliency is strategic planning and forecasting, which aligns all supply chain components and promotes visibility and agility. Supply and demand needs are better understood, and production is more synchronised as a result of strategic planning.
You should use past data, results, and relevant tools to analyse your business’ needs and further make accurate projections in terms of inventory, personnel, technology, and logistics requirements.
This interconnected, forward-looking approach assists businesses in better anticipating challenges, minimising the impact of disruptions, and improving overall operations and efficiency.
3. Incorporating Redundancies
Buffer capacity is the most fundamental way to improve resilience, whether in the form of underutilised production facilities or inventory in excess of safety stock requirements.
In theory, you can establish an adaptable supply chain by introducing redundancies across the network. However, while it can provide some buffer time to continue operating after a disruption, it is often a very expensive approach.
To avoid such high costs associated with it, you should invest in optimised inventory strategies that maximise order flexibility. These include managing extended lead times, strategic inventory positioning, maintaining safety stock to meet unexpected demand, and dynamic and localised replenishment models to guarantee that goods are delivered exactly when they are needed rather than when they are forecast to be needed.
4. Optimisation of Sourcing
Multisourcing is an excellent strategy in making a supply chain more resilient. It refers to the process of working with more than one service provider or manufacturer to meet demand. It eliminates reliance on any single supplier and ensures backup in the event of a supplier’s failure.
Apart from multisourcing, several businesses strive to eliminate geographic dependence on their worldwide networks and reduce cycle times for finished products. This is where nearshoring comes into play. It helps provide more inventory control and bring the product closer to the end consumer.
It is up to you to ascertain who you source from, but it is always better to have a diverse and dependable network of providers for maximum risk dispersion.
5. Standardisation of Processes
Interchangeable and standardised parts, manufacturing facilities, and procedures enable you to respond swiftly to disruptions by reallocating resources where they are most needed. Hence, you should aim to master the ability to standardise your processes by using interchangeable and generic parts in products, adopting identical or similar plant designs and processes throughout the company, and actively cross-training staff.
The benefits of standardisation include increased safety, uniformity, and quality. It provides seamless integration and optimised operations to improve supply chain management efficiency.
6. Adoption of Best Supply Chain Technologies
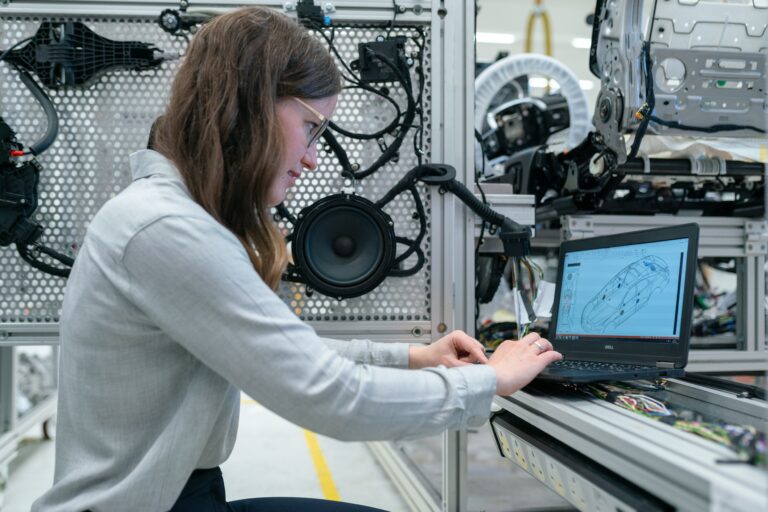
Digitalisation and modern supply chain technologies provide businesses with the resilience and competitive advantage they require to adapt rapidly to disruptions and opportunities. Here are a few examples of such technologies-
- AI (Artificial Intelligence): AI-powered supply chain systems can provide detailed procedural and operational insights by obtaining and analysing data from several sources. Predictive analytics and Big Data analysis can assist in forecasting risk and demand and recommending actions and responses across the company.
- IIoT (Industrial Internet of Things): An IIoT network in a supply chain comprises linked devices and things fitted with sensors and unique identifiers that allow them to send and receive digital data. They gather information and communicate with the central system which helps in better management of data and leads to more informed and better decisions.
- Robots and Automation: Robots and drones which are intelligently automated for speed, efficiency, and precision, can adjust their actions on demand to meet quickly changing needs. They also lessen the risk of injury to humans by relieving them of excessively dangerous or repetitive tasks.
Conclusion
Resilience means more than merely surviving a disruption in operations. A highly resilient supply chain not only survives adversity but also leverages it to innovate and strengthen its operations. Companies today are investing in highly skilled and knowledgeable people to build and manage their supply chains to maximise efficiency. They are taking all measures to optimise their capacity, standardise their procedures, and adopt best-in-class technology to achieve the edge needed to thrive in this competitive world and take their business to new heights.
Related posts
- 7 Proven Ways To Improve Your Supply Chain Management (SCM)
- How To Achieve Supply Chain Excellence In Manufacturing
- 8 Major Supply Chain Risks
- 7 Key Objectives Of Supply Chain Management (SCM)
- Top 9 Supply Chain Management Strategies For Business
- Top 10 Ways To Reduce Supply Chain Costs
- 7 Practical Steps To Improve Supply Chain Efficiency
- 9 Primary Benefits Of Supply Chain Management
- The Ultimate Guide To Supply Chain Risk Management
- Top 7 Supply Chain Risk Management Strategies
- 4 Major Benefits Of Blockchain In Supply Chain
- Top 7 Supply Chain Management Challenges
- What Is Green Supply Chain Management?