In the current economic atmosphere of limited stability and maximal competitiveness, warehouse productivity must be enhanced, while operating expenses must be reduced if any quantifiable success is secured.
The administration of your warehouse is the heart of your supply chain: it helps optimize procedures, make customers happy, and to maintain total inventory profitability. It’s easy to forget that inventory equals money. Therefore, it’s critical to keep costs as low as possible through good management while also giving everyone a clear picture of how the supply chain operates.
We have covered 10 strategies to reduce warehouse costs and make them efficient.
1. Inventory Transparency
Inventory transparency across your whole supply chain delivers clear and critical benefits, particularly as we welcome a new wave of online buyers, new retail patterns, and worldwide swings in purchasing. Unfortunately, business owners who are preoccupied with other obligations frequently ignore this. It can be highly stressful to rely on an employee’s memory to locate something.
Because every organization is different, ensuring inventory visibility across your entire supply chain at any moment necessitates a detailed assessment of problems, demand cycles, and distribution methods.
Every year, billions of dollars are lost in managing the warehouse processes. Some of the losses result from misplacement or theft, while the rest are the consequence of stock damage. Proper packaging and storage techniques aid in the prevention of inadvertent harm. Employees must also receive extensive training.
2. Efficient Storage
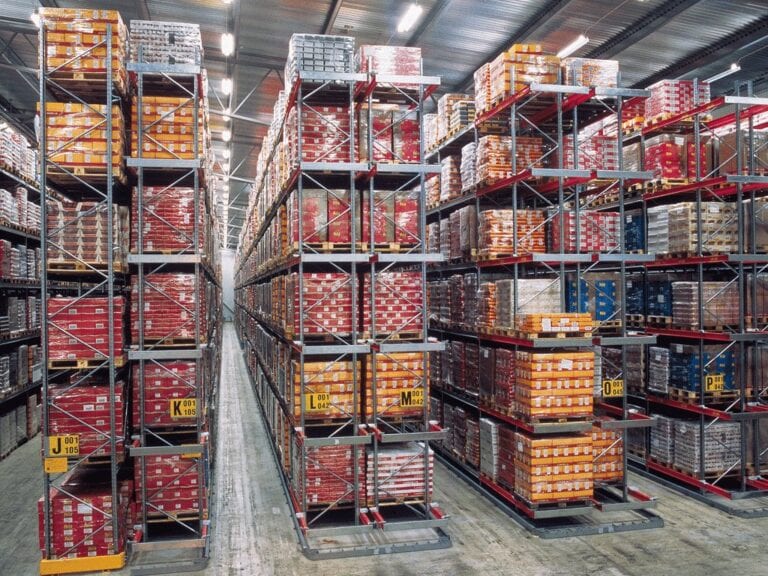
Optimizing your storage capacity may seem like a no-brainer, but it’s a complex process and often disregarded. It’s important to work with experts who use world-class layout and design ideas for optimizing warehouse storage for maximum efficiency.
An optimal warehouse will enhance inventory flow, prevent stock loss, and increase productivity for apparent reasons. These factors all contribute to greater overall efficiency. For any organization, this is terrific news because boosting profit and satisfying consumers are two of the results.
Smaller rooms are the most cost-effective, and by modifying storage processes, you may store more in less space. The sooner a product can be found in the warehouse, the sooner it can be put onto a truck for delivery. Discover the dimensions of the numerous forklifts required for each sort of merchandise. Sort your inventory by the aisle dimension needed for machinery access, and try to reduce the width of inefficient aisles wherever possible.
Racking is the most acceptable alternative for efficient inventory storage and optimizing storage space. This practice will increase the allowed square footage for pallets. The most frequent racking design is narrow and tall.
3. Benchmarking
Benchmarking can be defined as the procedure of continuously improving performance by recognizing, understanding, and applying excellent practises and processes found both within and outside the business. Benchmarking aims to improve any given business process by implementing best practices rather than simply measuring the highest performance. Companies frequently make the error of failing to align and define their benchmarking objectives around global industry best practices. Benchmarking your warehouse allows you to set objectives and track deviations from it. This gives you a clear picture of what is going wrong and where it is going wrong, making it much simpler to correct and optimize operations to get staff back on track, keep customers happy, reduce overheads, and enhance revenue.
A WMS can provide considerable benefits to your company across your entire supply chain, ensuring that you meet your business objectives.
4. Detecting Theft
Theft is a significant and pervasive problem that is causing inventory depletion. Theft is always difficult to prevent because the volume of goods moving through your system is enticing for staff at any point of contact. It can be challenging to determine whether a missing stock is due to theft or misplaced inventory, and where it may have occurred, making it difficult to identify culprits and stop it.
The red flags signalling warehouse theft include:
- Stock levels that do not match the sales records
- Staff rumours related to theft
- Drop in sales when particular staff members are on duty
- Unusual or missing invoices
- Stock being continually discovered in the wrong place (e.g. near the exit or loading bays)
5. Cross Docking
Cross Docking is a super-smart approach to cut warehouse expenditures. This is the direct transmission of the product from the supplier to the buyer, eliminating the intermediary and lowering prices at several points. The use of a cross docking terminal is straightforward. Incoming effects on your transportation vessels are unloaded and immediately moved to outbound vessels destined for client delivery. Cross docking saves time and money on product management, storage, shipping, and personnel expenditures.
6. Effective Slotting
By intelligently grouping goods based on picking tendencies, MHE limits, and warehouse structure, slotting optimization assists you in determining the ideal places for your inventory. This contributes to increased production, worker safety, and order accuracy.
When aiming to decrease costs in your warehouse, the first thing you should focus on is discovering and constructing your ‘golden zone’:
- The most convenient place in your warehouse
- Where your your fast-moving items should be kept/stored
- More significant, heavier, and slower-moving merchandise should be placed in the back.
This enables the employees in picking more quickly and accurately, while also cutting your overheads. With order picking accounting for up to 50% of your total warehouse operating costs, effective slotting optimization can help you save money
7. Use Modern Technology
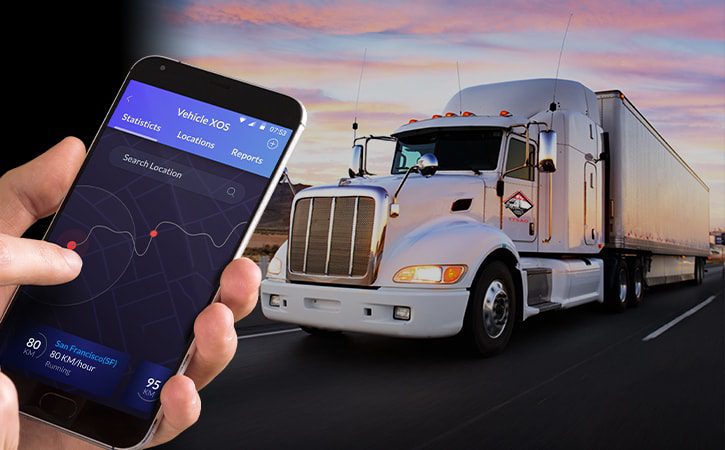
There are several methods for making technology work for you. If you do not already have a dedicated warehouse management system, now is the time to get one. Having vital information and specifications at your fingertips saves time and makes it easy to locate whatever is needed.
Consider launching a voice-directed selection system. Simultaneously, put-to-light and pick-to-light technologies will help to streamline warehouse activities. Installing RFID portals at strategic spots throughout the warehouse may also be a good idea. Making missing or lost merchandise easier to locate reduces total labour expenses.
The use of effective control mechanisms will help to prevent significant product misplacement. If appropriate, consider employing RF, RFID, or VDP. Install door guards and assign one or two to employees and guests entering and exiting the warehouse. Internal and external theft are both possible. Because of the monetary worth of product inventories, warehouses are high-value targets for burglars.
8. Optimized Picking
The cost of a wrongly picked product comprises the item’s purchase price, shipping costs, processing costs, and loss of customer satisfaction associated with returning the item. Correcting the mistake by picking, packing, and returning the correct product to the customer adds time to the overall project timeline.
Automation storage systems include advanced picking and real-time inventory tracking technology, such as light-directed indicators that specify the specific SKU location and quantity to be picked, resulting in up to 99.9% picking precision. The storage system reduces human error and improves inventory management. This will not only lead to fewer picking errors, but it will also save you a lot of money. The company’s client satisfaction will rise as a result, which can lead to more repeat business.
9. Efficient Labour Management
Labour consumes a sizable portion of every warehouse’s operating budget. Employees cannot be paid less, but reducing their dwell time will increase overall earnings. Time is money, and idle employees do not contribute to the coffers.
There are various other recommendations that should be implemented right away, for instance, paying particular attention to employee retention. To boost productivity, one may conduct cross-training and ongoing training seminars on new techniques.
10. Limit Your Product Damage
Costs can significantly rise if warehouse workers’ actions result in damage. Not only do the goods and products get damaged, but service also gets delayed. Any harm that causes a halt to your operations costs you money. To keep your warehouse safe, employ broad lanes, bollards, and guardrails to reduce damage and delays. Your product and facility are protected, but so are your employee’s thanks to these protections. Modern equipment, such as high speed/self-repairing doors, reduces downtime and damages, allowing you to return to the warehouse functions more quickly.
To be realistic about forklift accidents and damage in the warehouse, the question is not if they will happen, but when. As a result, your strategy should include prevention training along with crash-tested equipment and a safe as well as efficient workplace that can swiftly and effectively cope with these situations.
A Final Word
When you begin to investigate every aspect of how your business operates, you will be able to discover where cost-cutting measures are most needed. As each action is implemented and costs fall, the next logical step is to use savings to fund the more expensive options. Each adjustment will almost certainly lead to the discovery of more methods to minimize costs in related areas. Every warehouse is unique, and some ideas will not work for everyone. Just keep in mind that each measure has enormous long-term potential rewards.
Related posts
- What Is Warehousing?
- Cold Storage: Challenges & Opportunities
- 6 Major Benefits Of Bonded Warehouse
- Business Intelligence Solution for Intralogistics
- Everything You Need To Know About A Bonded Warehouse
- 11 Best Warehouse Management Systems (WMS)
- 8 Key Functions Of Warehouse Management System (WMS)
- 6 Common Types Of Bill Of Lading (BOL)
- 13 Most Important Warehouse Processes
- Warehouse Management System (WMS)
- 6 Major Advantages of Cold Storage
- List Of 11 Best Logistics Companies In India
- Top 8 Features Of Warehouse Management System (WMS)