The global demand for cold chain products is growing rapidly in the present times. As the worldwide market for perishable products expands, efficient and effective cold storage management becomes more and more critical.
Cold storage is a term used for refrigerated or frozen storage facilities, usually used to store food products, chemicals or any other items that require cool or frigid temperature conditions for their preservation. Cold storages have applications in several industries like pharmaceuticals, agriculture, chemicals, and many more.
Cold storages offer a myriad of advantages, some of which include cost savings, prolonged product life, customisable temperature settings, more storage space, etc. But, to derive such benefits, proper management of cold storage is imperative.
The most significant cause of concern in a cold storage is the damage caused by the extreme cold. If not properly dealt with, it poses a risk of wear and tear of the equipment, affects employees and the tools they use like scanners and computers, and can also cause machinery to require more frequent maintenance. Yet, low temperatures must be maintained perpetually in a cold storage unit to ensure that the temperature-sensitive products inside remain fit for use. Products may include lifesaving pharmaceuticals or food that either lose their effectiveness or become unsafe to consume when stored at warmer temperatures. Hence, it is essential to manage a cold storage in order to keep temperatures low, equipment functioning, employees healthy, and products safe for use. Following are the 8 best practices that you can employ to manage your cold storage units efficiently-
1. Adopt Automation
Cold storage space is costlier than other types of warehouse space, primarily because of the costs associated with keeping the space at a constant low temperature. And as the cost of energy, land and labour continues to rise, cold storage users are increasingly seeking automation to control costs.
Automation can optimise the available cold storage space by improving cube utilisation. Employing high-density pallet racking systems with pallet shuttles, Automated Storage and Retrieval Systems or ASRS helps make optimal use of vertical space.
Automation can also minimise the need for human labour, leading to substantial savings. The use of Autonomous Guided Vehicles or AGVs for shuttling products through the warehouse along with automated palletisers and depalletisers makes it possible for cold storage units to operate with a much lesser number of employees. This has many benefits beyond just cost savings.
2. Maintain Temperature Ranges
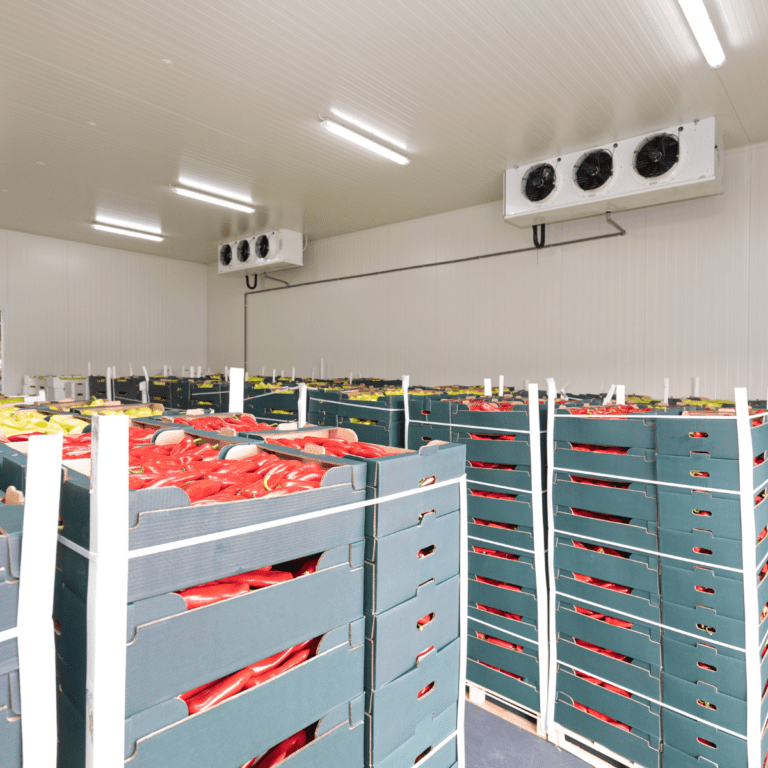
A single cold storage warehouse does not usually hold just one type of product. Instead, it simultaneously stores different products that require different temperatures. For example, vegetables are stored below 12°C, milk and other dairy products are kept just above the freezing point at 1°C, meat products are held just below the freezing point at -2°C, and ice cream is generally stored at –23°C.
Temperatures must be regulated in each part of the cold storage unit and must remain within their set ranges. For example, refrigerated products must remain refrigerated and frozen products must remain frozen.
The challenge of storing all these products in the same cold storage can be dealt with by creating a barrier between the respective temperature zones. Hence, for warehouses that need multiple temperature zones or where the types of products being stored change periodically, a flexible, low-risk option can be a modular insulated curtain wall system that can be set up in and moved from one building to another as per the requirement.
3. Minimise Heat Loss
After making sure that different temperature ranges are set in the cold storage unit, it becomes necessary to ensure that such fixed temperatures are maintained, and there is no heat loss. Minimising heat loss is crucial not just to achieve more energy savings but also to avoid spoiling the contents of the cold storage.
The transfer of heat must be carefully restricted to prevent its flow from high-temperature areas to lower-temperature zones. It is a complicated task in a cold storage warehouse as new products are regularly entering storage, and the warehouse may need to be routinely reconfigured.
High-speed or rapid doors and strip doors are effective solutions to this problem. They contain refrigerated air with great efficiency and at the same time allow unhindered access to people and vehicles to all areas of the site.
4. Use Suitable Equipment
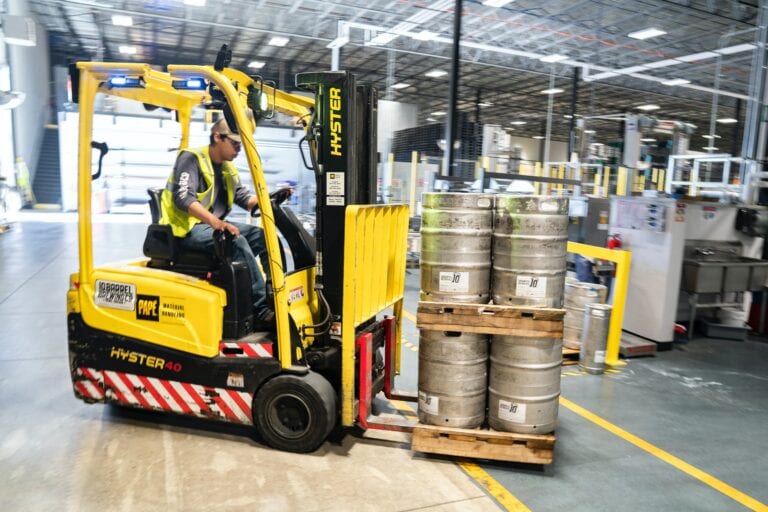
Various tools, machines and equipment are used in a cold storage warehouse, like barcode scanners, computers, sensors, forklifts, pallet jacks etc. To perform the desired functions, such equipment should be designed or modified according to the low temperatures they are supposed to function in. For example, it can be hard to operate a touchscreen when you are wearing thick gloves. For this reason, touchscreens on cold storage equipment are made sensitive enough to respond easily to a gloved touch, and the buttons on scanning devices are made big enough to be felt through work gloves.
Moreover, the condensation that forms when devices are moved from one temperature zone into another can short out electrical equipment like scanners. Handheld equipment and electric forklifts are manufactured with seals designed to withstand such temperature changes.
Constant exposure to the cold also has a severe impact on battery life, resulting in a 40% to 50% degradation to the life of a battery. Hence, higher voltage batteries need to be used to extend their use cycle.
5. Ensure Employees’ Safety
Providing employees with proper personal equipment is a necessary step that ensures their safety and smooth functioning of the cold storage unit. Providing them with insulated coats, pants, gloves, and other gear they require to stay warm is a cold storage management practice that has several positive effects and improves efficiency throughout the cold storage warehouse.
Employees should also be trained to familiarise themselves with the cold working conditions, to minimise any health risks to them and also to make sure that they do not compromise the efficiency of the operations. For example, if employees are prone to holding doors open to let the room temperature air in to keep themselves a bit warmer, temperature protocols would be violated, and a lot of refrigerated air may be lost. So, the best practice is to ensure that employees in cold storage warehouses are trained well and can always find the appropriate gear for a cold storage zone.
6. Manage Energy Demand
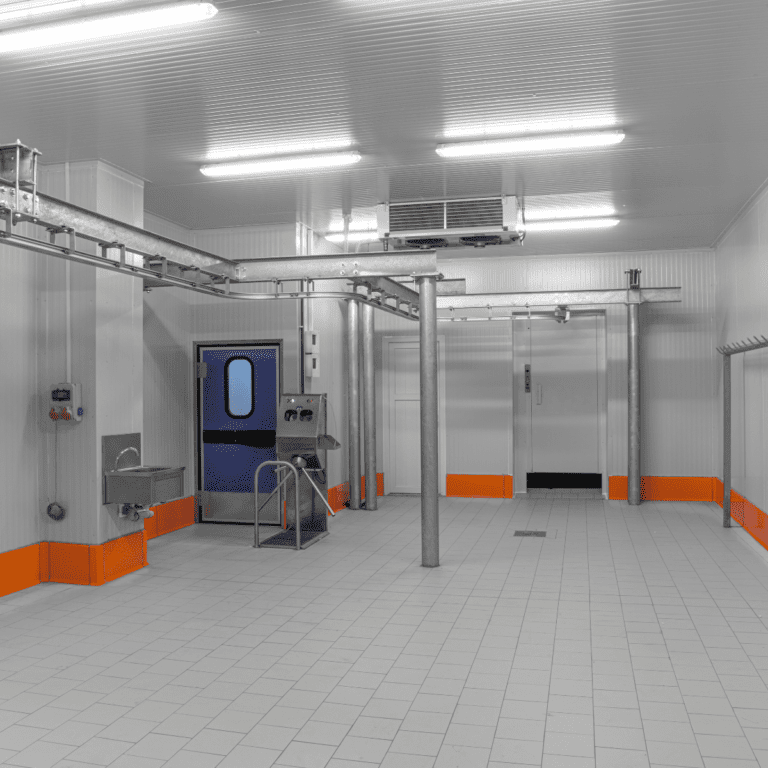
Energy savings is a prominent consideration in cold storage simply because it is more expensive to cool air than to heat it. While appropriate building design and automation system selection can minimise energy consumption in a cold storage unit, managing demand can also lead to savings. Controlling energy costs during high-demand periods minimises the impact of surge pricing and can bring down costs on a per-kilowatt-hour basis. However, the challenge is that consumption and costs are highest on high-temperature days when the thermal load is at its peak.
The key is to employ advanced control algorithms and sensors that allow smart energy management. Cold areas are over-cooled during periods of low demand, such as overnight, creating a thermal buffer that minimises cooling requirements during peak periods.
7. Maintain Proper Records
The contents of a cold storage warehouse are susceptible to temperature changes. That’s why one of the most vital cold storage practices isn’t just keeping the products cold but also keeping an accurate record of the details of their temperatures.
Technology plays a huge role in this. Temperature sensors are used to automatically keep track of temperature, trigger alarms, and identify potential lapses. The use of sophisticated databases allows this collected data to be linked with products at the load unit level via Radio Frequency Identification or RFID tracking without scanning every carton and stock keeping unit.
These technologies allow accurate and transparent records to be maintained so that anyone in the supply chain can access them. Keeping accurate and up-to-date temperature records for all products in a cold storage is one of the best practices in cold storage management.
8. Keep a Contingency Plan
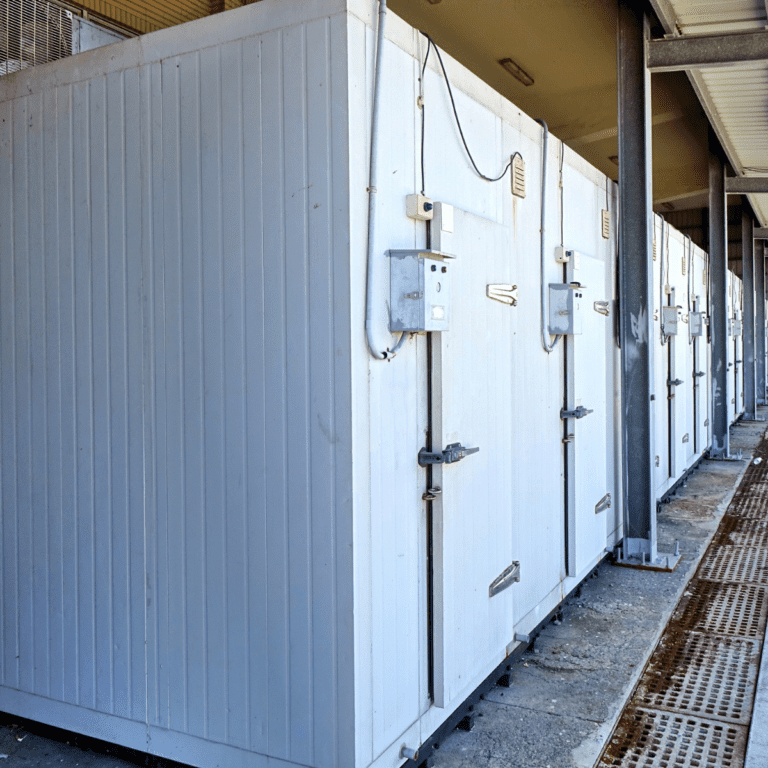
Even with the best technology, an unpredicted delay or re-routing could jeopardise your shipment’s stability. Shippers should work closely with their transportation partners to devise contingency plans that map out a strategy in the event of unforeseen circumstances.
Contingency planning is also a key factor in managing your cold storage. If a truck breaks down, a refrigeration unit stops working or in the case of a power outage, you must be ready to respond immediately.
To ensure efficient cold storage management, all parties involved must cultivate a strong partnership and have an excellent working knowledge of the best practices for cold chain handling and transportation.
The Bottom Line
Cold Storages are increasingly becoming a crucial part of the supply chain. When maintained and managed efficiently, they offer various advantages ranging from prolonged product life to savings in cost. Good cold storage management practices are improvements in procedure and equipment that can lead to substantial savings and greater profits down the line. Some of the best practices in managing a cold storage include automation, minimising heat exchange, using suitable equipment, maintaining up-to-date records and keeping a contingency plan handy. Adopting such practices might not yield instant profits, but when even a minor improvement is diligently implemented, it can pay off substantially, given enough time.
Related posts
- 6 Major Advantages of Cold Storage
- 6 Major Types of Cold Storage
- Industries And Applications of Cold Storage
- 11 Best Warehouse Management Systems (WMS)
- Cold Storage: Challenges & Opportunities
- An Ultimate Guide To Inventory Management
- How to Sell on IndiaMart in 2024
- Four things to consider before buying a storage space in Pune
- Top 10 Transport Companies In India
- Top 12 Transport Management Softwares For Logistics Companies
- 10 Best Cold Storage Companies In India
- Going Up: Logistics Leaders Solve Warehouse Space Constraints
- Top 10 Latest Supply Chain Trends In 2024