“Expanding your warehouse isn’t the only way to maximize your revenue from space. There are proven ways that ensure maximum space is utilized at your warehouse facility. Did you know a warehouse that is said to be exhausted in terms of area, is yet 25 per cent unexplored?”
Warehouses have evolved from basic godowns to advance facilities that are capable of functioning at high productivity levels.
Businesses and manufacturers in today’s time are much reliant on optimal storage features and services to regulate the supply chain efficiently.
The high demand for warehouse space in India is the primary reason why even fully occupied warehouses must opt for maximizing their space utilization.
As per evaluation, when a warehouse is 80–85 per cent occupied, it suffers from a setback in terms of efficiency levels. Inappropriate inventory management leads to restricted mobility of goods and mechanical equipment within the warehouse facility.
Limited aisle space and reduced movement at warehouses also involves risk due to damage or loss and indirectly affects the supply chain.
It’s not always the smartest decision to opt for expansion when there are several ways to optimize inventory management and ensure maximum space utilization at your warehouse or Distribution Centre.
Effects of your warehouse reaching capacity limit
Companies and warehouse owners majorly focus on enhancing operations by streamlining the process of picking goods and reducing storage time of additional stock.
If we dig deeper into the multi-channel operations carried out at a warehouse or a Distribution Centre, usually when a warehouse is 80–85 per cent occupied, efficiency tends to plummet in terms of mobility and storage.
Congestion at your Distribution Centre often disrupts the various in-house operations, leading to an increase in costs and a cooldown in warehousing operations.
As a manufacturer or a warehouse owner, it is your role to plan out a legitimate inventory storage mechanism by addressing various concerns such as:
- Is it possible to create a report based on the age of the inventory at your Distribution Centre and liquidate overstock?
- Are you thorough with inventory reports that show the ‘weeks of supply’ by SKU and the inventory turnover?
Keeping track of your inventory turnover and inventory reports will provide you with an apt judgement of the number of weeks it would take to release off your inventory.
Why do Distribution centres reach the storage limit?
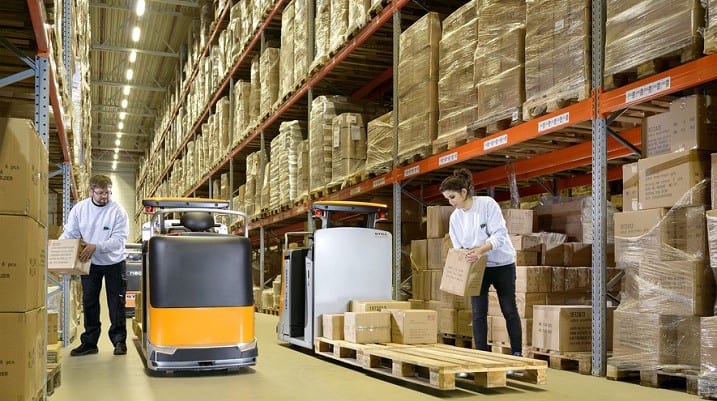
Once a warehouse or a Distribution Centre reaches its threshold problems such as blocked aisles, damages and loss in productivity starts popping-up in the macro.
Although many factors come into play. Factors such as demand and supply, seasonal peaks and ghosted inventory are the primary factors that lead to congestion and less space.
Demand and supply for products are one of the core reasons that lead to an overstock of at your warehouse. Every time the ‘demand’ is at its peak, businesses and manufacturers aim at storing additional stock of products — as they sell faster.
One of the leading contributors to the lack of storage space is also when you don’t adequately plan inventory storage with time boundaries. A Distribution centre generally requires a stock worth of two months. At times, the clients end up buying stock worth of six months leading to excess inventory stock.
Ghosted inventory is also the most crucial reason why warehouses and Distribution centre fall back on inventory management and other in-house operations. Ghosted inventory are those that lay idle for several seasons. A stock that is capturing space and can be liquidated.
What can we do to maximize space utilization?
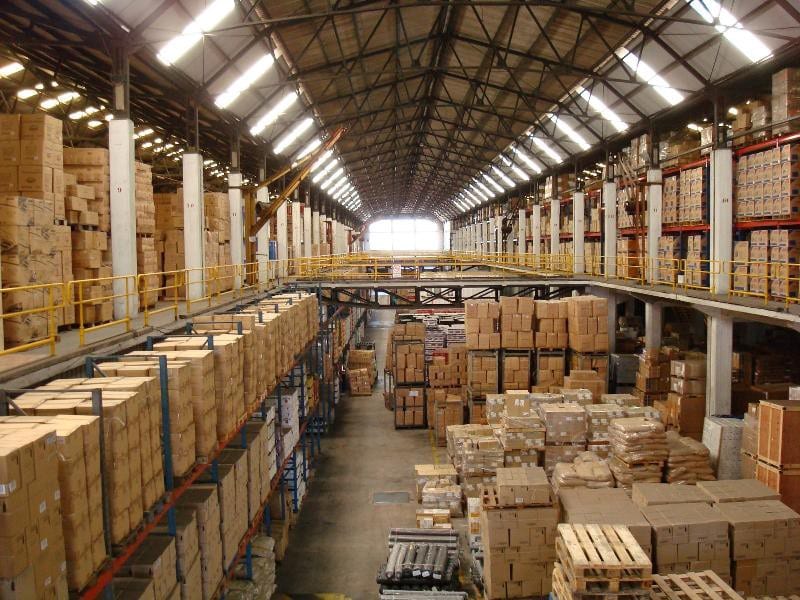
Increase Your Vertical Space
One of the simplest and most effective ways to optimize the usage of your existing space is by extending up racks.
As a warehouse owner, it is crucial to know the maximum vertical space you can rack up. Generally, warehouses have in-built fire suppression sprinkler system, and one can extend up to 18 inches of the residual area.
How About Installing a Mezzanine?
Warehouses or Fulfilment Centres are typically high-ceilinged buildings. In warehousing terms, A mezzanine is a semi-permanent structure that can be dismantled and relocated within the warehouse.
The purpose of installing a mezzanine is to provide a shipping or staging area for incoming and outgoing inventory at all times. A mezzanine installed above the floor-level can increase floor space up to two folds.
Make Minor Adjustments With Aisle Width
At a Distribution Centre, aisle width falls in the range of 10–12 feet. As a part of being the warehouse owner, one should focus on reducing the aisle width anywhere between 5–8 inches.
It might require better planning, but in the long run, it saves 15–20 per cent space that usually remains unexploited.
Before heading to reduce aisle space, one must evaluate that the aisles are spacious enough to accommodate lifting machinery and facilitate lifting operations.
Enhance Your Storage Medium
Another effective way of optimizing inventory storage can be increasing the depth of available space, in other words, utilizing higher density mediums such as a double-deep rack instead of single. Double-deep racks would ensure maximum space utilization depth-wise.
Although increasing the density of storage have certain limits such as first in, first out. Higher is the density of your racks, the more difficult it is to handle and move the products that are in first.
Confine Products That Arrive in Half-Pallet Quantities to Half-Pallet Locations
An innovative way to ensure maximum space utilization is dedicating a location for pallets that arrive in partial quantities.
Organizing and condensing your pallets allows further space for additional pallets; this allows adequate storage of more products and less grey space.
Leverage the Benefits of Your WMS For a Directed Put-Away
As a warehouse owner, it is necessary to ensure directed put-away of incoming stock.
Use your warehouse management system and forbid the rule of dumping stock directionlessly. Use the feature of directed put-away, which knows the best locations suitable for pallets in the warehouse.
Make Full Use of The Unutilized Space
Underutilized space or grey space is that area which still holds the potential to be used in some way or the other.
Every warehouse or Distribution Centre has grey spaces, you can find them at shipping doors, or the staging area for inbound and outbound material that hasn’t been processed yet.
Exploiting these grey spaces and utilizing them ensures maximum space utilization and smooth logistics operations.
Store Your Products in Trailer For Short-Term and Seasonal Needs
Storing inventory in trailers might not be the wisest of options available, but is a great temporary solution to ensure your warehouse doesn’t run out of space and operates efficiently.
Storage of seasonal products is best suited for trailers. Often warehouses bring containers at seasonal times and pay demurrage charges to optimize storage options and other in-house warehousing operations.
How is Stockarea Helping?
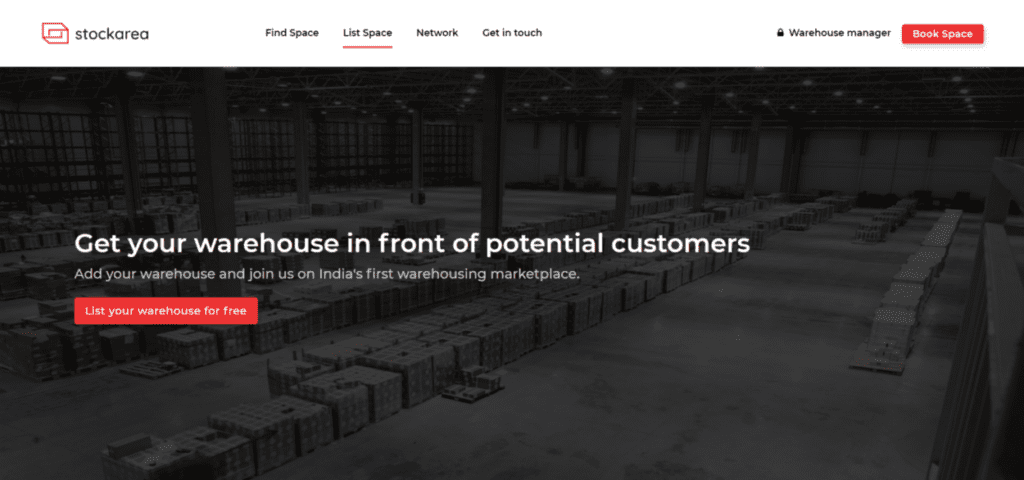
At Stockarea, we aim at creating a culture where filling up your warehouse space is quick, easy and hassle-free considering optimal inventory management and higher efficiency levels at your warehouse facility.
“Stockarea is India’s first digital warehousing marketplace visited by thousands of businesses, manufacturers and retailers looking for short-term and long-term warehousing solutions and warehouse spaces.”
Warehousing services providers and 3PL providers can leverage the cashflow-potential of free space at warehouses and maximize warehouse space utilisation, ensuring a warehouse remains high on value, revenue-generation and productivity levels.
To conclude…
Storage space issues are something that currently doesn’t have a permanent, once-and-for-all solution. But as warehouse owners, we can take necessary and calculated measures to make sure our warehouse is generating utmost value, in terms of both storage space utilization and efficiency of the inbound warehousing operations.
Secondly, the efficiency of your warehouse is an aspect that requires continuous evaluation and innovation. There can be more ways than mentioned above to maximize space utilization – something that needs detailed attention and innovation.
Related posts