In a highly competitive environment, enterprises and manufacturers must be acquainted with the various methods that are incorporated at warehouses for the storage of inventory which is optimal and saves on storage cost.
Warehouse companies understand the dire need for implementing storage methods that suits their customer’s demand most appropriately.
To have complete information about storage methods is to be able to choose the right techniques and incorporate them and leverage the benefits that come along the way which comes with different storage methods.
Types of Storage Methods
1. Pallet Racking
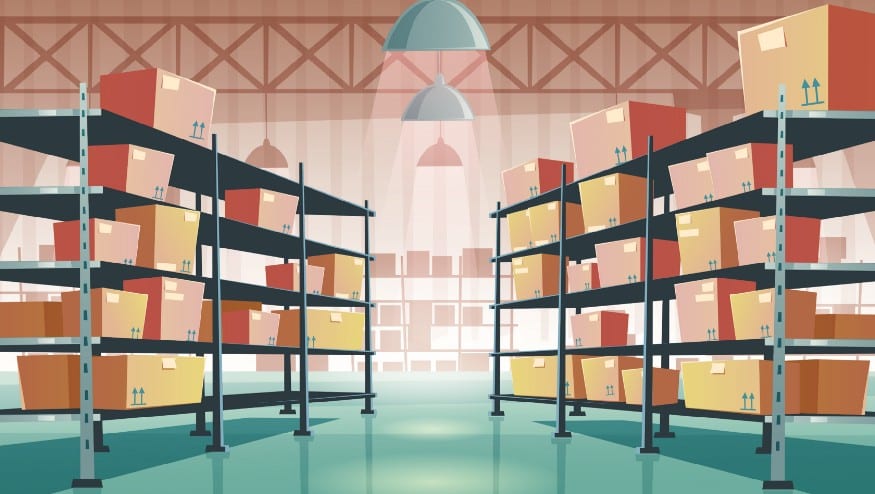
Racking is the most basic method employed in a warehouse. This technique involves the utilization of pallet racks, that can be single or multi-levelled.
Pallet racks are the most fundamental component at warehouses used for high stacking of palletized goods.
The structure of a pallet rack comprises vertical columns and horizontal beams. The upright column of a pallet rack serves the purpose of exploiting the vertical space at a warehouse and varies in height, depth, and design based on storage needs and infrastructure.
Whereas, horizontal beams are the load-bearing components of the pallet rack that provides a surface area, where goods are stored and placed with appropriate lifting machinery (forklift) from time-to-time.
Various benefits of pallet racking at your warehouse are:
- Pallet racking optimizes inventory storage at your warehouse by allowing you to exploit the vertical space hence increasing storage efficiency and storage density.
- New generation pallet racking systems are equipped with slant-back support frames, especially in driving-in storage systems. This very trait ensures the safety of goods from damage and loss.
- Racking systems are generally expandable and as a business, when your inventory grows — you can accordingly adjust the pallet racking system.
It is essential to know your warehouse thoroughly before installing any storage system. At times, the pallet racking system is not advisable as it covers a substantial amount of floor space, which leaves very less aisle space for lifting machinery to operate.
The pallet racking system can also prove to be expensive for storing goods in high volume. As a warehouse owner, it is necessary to read these yellow signals and choose the most appropriate storage technique that best suits your warehouse.
2. Single Stacking
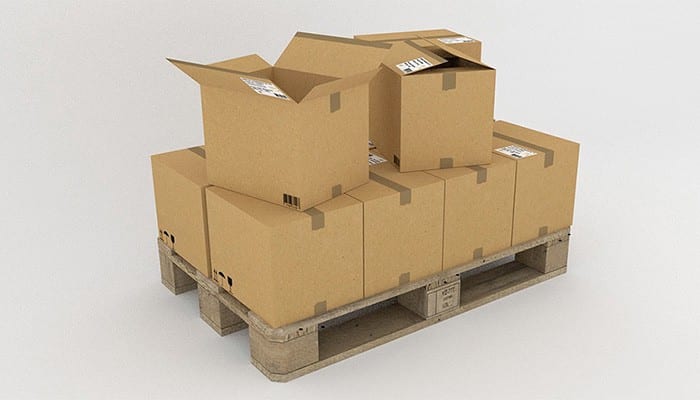
Single stacking is most commonly practised method at a warehouse for the storage mechanism due to its meager setup costs and flexibility. In this method, pallets are stored and handled directly on the floor space instead of dedicated storage equipment.
Single stacking typically serves the purpose of storing goods that are high in value and require special attention throughout the storage period, to prevent any damage or contingency, resulting in significant losses.
Single stacking is one of the oldest forms of storing high-value goods and only involves a ‘single’ row of pallets or cartons covering a flat surface.
As a warehouse owner, it is necessary to be acquainted with the various limitations that a single stacking system possesses.
- Since a single stacking system only utilizes floor space, it promotes low-density storage. In other words, fewer goods take more space causing inefficiency in other in-house operations.
- Single stacking methods also cause obstruction for lifting equipment to operate smoothly, which at times involves risks due to damage or losses.
Although the method stands out to be effective only in some instances, as a warehouse owner, it is your role to study the cases that require single stacking and optimize your warehouse accordingly.
3. Double Stacking or Block Stacking
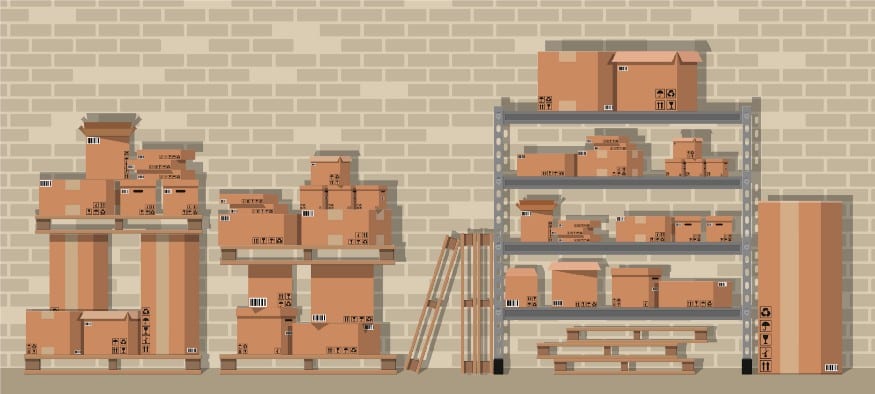
Double stacking or block stacking ventures the utilization of the vertical space available after the first layer of stacking.
Although, the height up to which one can stack entirely depends on the material each block is holding. Various factors come into play while planning to implement block-stacking at a warehouse facility.
Factors such as crushability, load weight, load stability, pallet conditions, safety factor, weather conditions, and allowable clearance heights are keystone components that require to be studied before determining stack levels for your goods.
Double stacking or block stacking is an effective method if it goes in sync with the goods that need to be stacked.
Block stacking doesn’t require dedicated storage equipment but is instead a system of multi-layered stacking of one block over another. Although, block-stacking cannot be applied everywhere and at every condition, because –
- The fundamental limitation to double stacking or block stacking is that one can access SKUs only in the last-in-first-out (LIFO) method.
- Even though block-stacking enables vertical storage, it still demands higher horizontal space for the storage of more goods.
- Block stacking is product sensitive and is a method that tends to fail for fragile products.
4. Pallet-less Stacking
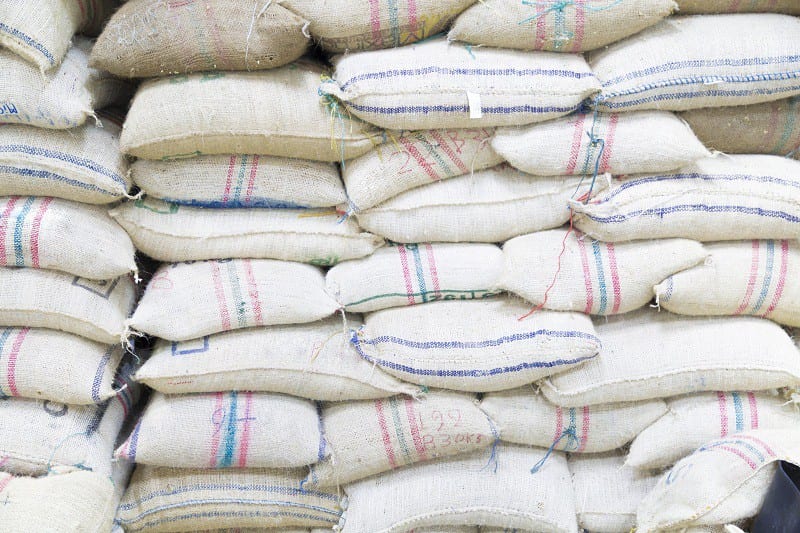
Pallet-less stacking is a process that aims at the complete removal of pallets for the storage of goods.
The method involves utilizing the floor space and stacking cartons or crates one over the other. Stacking one box over the other enables the usage of vertical space.
Pallet-less stacking also allows one to store goods based on the order.
- FIFO: the method of pallet-less stacking allows the first-in-first-out form of inventory management, which implies that the goods that enter your warehouse in the first place are goods that also exit the warehouse primarily as per requirement. Appropriate execution of FIFO ensures proper rotation of your stock. For example, FMCG products.
- LIFO: The last-in-first-out technique to stock management is contrary to the previous method. LIFO refers to the process where the products that have recently entered the warehouse are the ones that are cleared first. This method is suitable for products that are homogenous or imperishable. This method serves considerably well for goods that are seasonal or perishable. For example, commodities.
Although there are limitations to this method, and the technique is entirely case sensitive. Distribution of goods depends on the availability of space at your warehouse, and for the supply chain to operate smoothly, it is necessary to optimize the in-house functions of a warehouse.
In a nutshell
Warehouses have evolved from basic godowns to structures where appropriate storage methods are implemented for maximum efficiency.
Executed in the right manner, storage methods ensure products are easily accessible and there is a prevalent ‘flow’ of logistical operations. As the businesses are matching up with the pace of evolving market demands, so are the storage methods within warehouses.
Stockarea is a single network of warehouses all across India. At Stockarea, it is quick and easy to connect with customized warehousing and distribution solutions anytime and anywhere. All the warehouses enlisted in Stockarea’s network are compliant to best storage practices that enable efficiency and reliability in logistical operations. With a dedicated support team and a single operating procedure for all warehouses, we ensure warehousing is simple, straightforward and convenient for your business. Partner with us today!