Warehouses deal with numerous processes whose optimisation is necessary for a well-functioning warehousing system. They help in managing the order rates and in cost- control. They are also the main activities that take place at a warehouse. Companies gain an edge over their competitors as efficient warehousing services always mean better order fulfilment and, in turn, customer satisfaction. The following is a list of key warehouse processes that you should understand.
1. Receiving
The first process that takes place in a warehouse is the receiving. As the name suggests, this is the step in which the product reaches the warehouse. The workers are supposed to cross-check the items that have been received and ensure that they are of acceptable quality and quantity. This is carried out using a predetermined system wherein the ordered items are mentioned beforehand and tallied later on, once the order is received. It may be stored in the inventory(for the long-term) or the main storage area(for the short-term) based on its requirement.
Once the inbound items are received, it is the responsibility of the warehouse to keep it safe until the order goes for dispatch. Issues in this step may cause problems in the steps that will be carried out moving forward.
Warehouses must ensure that there is no overcrowding of goods. In order to move the goods faster, they can use power pallet trucks and conveyors. Such technologies make functioning easier. Another software that improves efficiency is the labour-management system and dock scheduler, as it helps in the proper allotment of labour based on order size.
2. Put-Away
Put-away is what takes place after the receipt. The received products are supposed to be put in a storage place, and this process is called put-away. It is done by the put-away staff who receive a notification about this requirement on the receipt of the inflow. Proper planning of this process helps in the appropriate use of the storage space and the safety of the workers. Several accidents can be avoided by an efficient put-away procedure. The cataloguing of items is easier through this process. Only after the goods are stored in the correct location and accounted for, the process is considered complete. The size and weight are considered primarily while deciding the storage place.
Slotting and space management systems are softwares that reduce manual hard work by automatically assigning storage spaces to product based on the requirement. They assist in full space utilisation and the least time consumption. The appropriate execution of this process is necessary. Otherwise, the goods may get ruined for future procedures.
3. Picking
Picking is the costliest process of warehousing. In this process, the goods are collected for the fulfilment of customer orders. The accuracy of this procedure is essential for complete customer satisfaction. Making sure that the right order makes it to the correct delivery location on time is vital. For this, picking the correct goods on time is critical on the warehouse’s end.
There may be two proceedings after the pickup. One may be simply sending it off to the packing table for dispatch, while the other is where the picked goods are allotted to specific group orders or individual orders. Often, orders are picked up as soon as they are received, known as the real-time ordering system, while sometimes specific pickup times are preassigned and several orders are dispatched on those particular time in waves.
Put walls, put-to-light systems, goods-to-person systems, and cross-belt sortation systems are new technologies being implemented with the advent of online shopping. They help in the proper handling of small bulk orders. Essential technologies such as mobiles and wearables allow the workers tally their lists wirelessly and more efficiently.
4. Packing
Packing is the process of preparing the picked items for shipment. Workers have to pack these items and ensure that they are safe even after they leave the warehouse. Goods are placed in boxes or poly mailer, and specific packing material is added along with a label. The various batch item and manufacturing codes should be added while packing using stickers. The box must be lightweight, easy to carry and handle.
The warehouse officials should carry out a quality assessment at each step. Choosing the appropriate kind of packing material and method is necessary based on the product’s need. Specific codes should be used to trace the goods back to the systems to prevent theft and misplacement. Accumulation of goods from different warehouse sections to complete certain orders is also carried out while packing.
Specific softwares analyze the already existing data present in the system to determine the appropriate packaging for the particular goods. These have helped optimise the packing process.
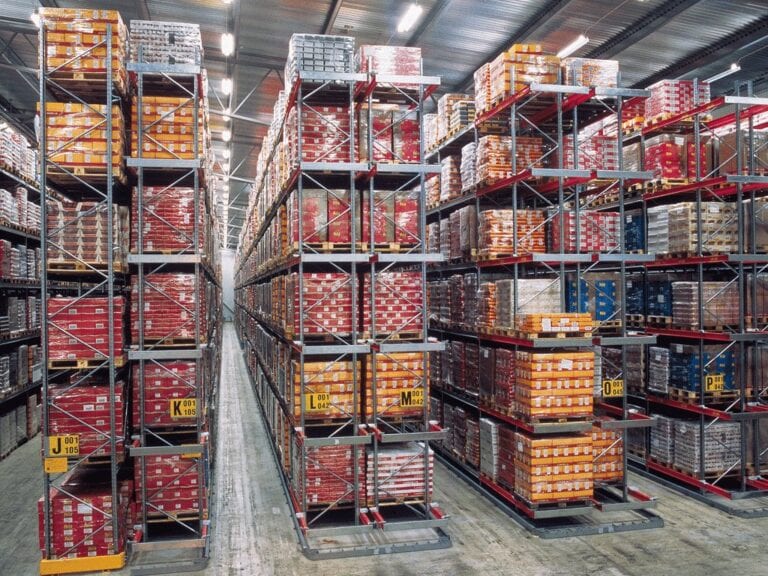
5. Dispatching
The principal governing factor for the dispatching process is the time of delivery. Based on that, the operations manager plans the packaging and dispatch procedure. If this process is not carried out, it will lead to delayed delivery times and loss of customers. However, at the same time, a balance is necessary. If goods are packed too ahead in time, it may lead to overcrowding of conveyor belts or similar structures. Whereas a late dispatch may lead to late deliveries, as mentioned above. The efficiency of the dispatch process can be instrumental in forming the company’s image as it is based on this process that the delivery time is met.
Whenever there are orders assigned to certain specific delivery routes, firms tend to use their own delivery services. However, in the generic routes, delivery services are outsourced.
6. Shipping
Shipping is the first step for the product on the path to reach the customers. In this process, deliverymen categorize and group the orders. They are supposed to take the shortest routes for the shipment. Along with this, they have to deliver the right order to the designated customer at the proper address. Also, they ensure that the product stays intact with no damages on the way. The best way to manage this is by packaging the goods for shipment near the shipping docks.
Many times companies use outsourcing techniques for their shipments. They hire certain shipment companies to take the orders from the warehouse to the customers. Furthermore, businesses are supposed to arrange for methods to track their orders while they are on the way to their destination.
Labour management systems, shipping applications and devices are the methods that companies can use to optimise the shipping procedure. Computerised systems help improve efficiency and reduce the burden on human labour. Some applications have instruction manuals on the loading and unloading procedures as well.
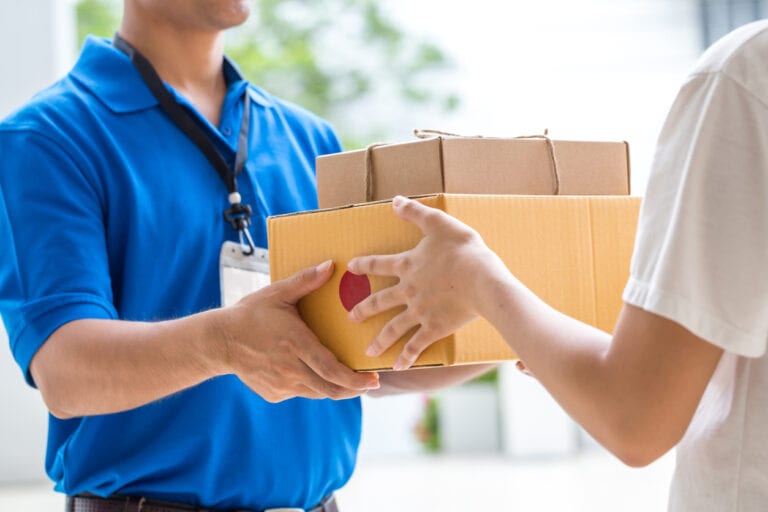
7. Kitting/Dekitting
The kitting process includes collecting all items of an order individually into a single box or “kit”. It is followed by packing them together instead of picking and packing each item separately. Hence, the company creates a single unit in the inventory.
Through this process, the time taken to complete each order is reduced. The staff can avoid unnecessary efforts on processing items individually. Thus, the process of order fulfilment and inventory becomes easier. Companies gain a competitive edge due to the increased worker productivity and efficiency brought about by the kitting technique. Since this process is completed in one go, the scope for error in completing an order is reduced. The time and material wasted on packing each item separately in boxes is saved since the workers can now pack one custom box directly.
The dekitting process is an exact opposite of the kitting process. All the items that are part of a kit are de-assembled and placed separately in their designated places. These individual items can then be shipped away for specific orders within the country or abroad. This process is generally employed when there are several small shipments. However, they are not enough to be delivered to a particular place.
8. Casing
Casing is when goods are picked up directly while stored in their cases from their respective storages. Mostly, fragile items are stored in such cases. Companies devote parts of their warehouses towards picking up these cases along with the goods.
Traditionally, casing has been considered a job for manual labour however now it has been modernised. The use of automated conveyor belts has been prevalent for the transfer of large cases.
9. Inventory Tracking
Inventory Tracking is the process of accounting for all items stored in the inventory of the warehouse. An inventory mainly consists of the stock of goods already present in a warehouse. While tracking, one has to consider the inflow and outflow of the items based on the previous and new orders. Hence, it is like a consolidation of information regarding all goods present in a warehouse. At the same time, they have to assess the speed at which items leave the inventory due to sale. Hence, the two important components of inventory are – time and speed of inventory inflow or outflow.
One can take two approaches while carrying out inventory tracking – serial or lot tracking.
- Serial tracking – Used for expensive items that are sold in lesser quantities.
- Lot tracking – Used for budget-friendly items sold in large quantities.
Several softwares that help in such management have been developed recently. These softwares may work on ERP systems or stand-alone systems. The primary functions, however, remain inventory management. Based on the company’s specific needs, they can choose to buy suitable software.
Warehouse managers play a significant role in inventory management. By appointing them, the entire process becomes organised and less prone to systematic errors.
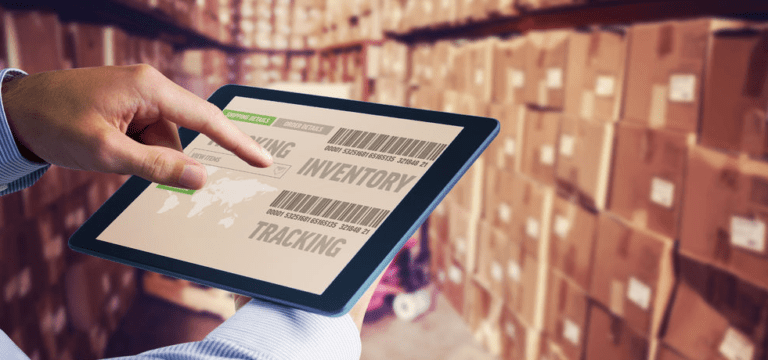
10. Value-Adding
Value-adding is the final step that gets the product ready for sale. In this process, the warehouse company adds certain features as final touch-ups. It can be a complex process as several different products may be a part of an order and need separate touch-ups. At the same time, there are goods made of several components whose value-addition process becomes even more complicated. Through this process, they aim to increase the revenue or even decrease the cost of production. The cost improvements reduce the money to be paid by the customer hence increasing customer satisfaction.
The warehouses can also play a significant role by decreasing the time from receiving the inbound items to order shipment and the amount of inventory. Also, better staff regulation and enumeration of inflows and outflows help in a more systematic process, hence, adding value. Warehouses have to ensure they minimise the discrepancies between receiving the product and its shipment for order fulfilment. Thus, a warehouse not only adds value to the product, but its existence in itself should also be of value.
11. Returns
Whenever customers are not satisfied with their products, they put up a return request. After this, it is the responsibility of the warehouse to arrange for the pick up of the products. They are supposed to be prepared for such situations by allocating space for returned items in the warehouse. If products are damaged and need to be discarded, manual accounting of the same is necessary. However, if goods are in shape, they may be recorded electronically and simply put up for reuse or resale.
The increasing online shopping trend has also increased the number of customers returning items. It has further created a responsibility on the warehouses to create a proper system for the return process. Within this, keeping a separate cost analysis system is also necessary. It will account for the extra expenses on return processes such as picking, repair, repacking etc. Software and technology have helped in this process as they reduce manual error as well as labour.
12. Reporting and Analytics
An essential part of the warehouse process is the reporting or recording of all happenings in a warehouse. Starting from the arrival or receipt of the order to the shipment followed by the return procedure, all should be accounted for. There should be a proper database for all the inflows and outflows of the warehouse, along with the costs incurred. It helps in estimating how many resources and labour the company may require. All transactions and payments must be recorded and tallied. The number of staff and their salaries for each department must also be catalogued and supervised. Supervisors can also check workers for safety training and the possession of licenses and certificates required to run specific equipment.
Next, another process is that of analytics. Proper assessment of the functioning of the warehouse is necessary. Whether the workforce is efficient and fulfilling their duties and jobs has to be checked. Quality and hygiene standards need to be met. Tracking inventory and making sure that there is proper utilisation of space is also essential while storing goods.
13. Damage control
Ensuring that the goods stored in the warehouse are protected from all damage is necessary. In a way, this is a part of the contract when a warehousing company takes up the responsibility of storing goods. To fulfil this responsibility, warehouse staff should store all goods based on their size and weight. Specific protection racks should be provided for fragile goods. At the same time, staff training to manage all accidents should be carried out before recruitment. A clean and hygienic environment is also necessary to prevent damage to food products or perishable goods. Warehouse services should also consider the weather of their location and build infrastructure accordingly. It is essential for edibles. Lighting should be well maintained so that no errors or accidents may take place.
Stretch wraps and safety traps are also used to prevent goods from damage.
In conclusion, the efficiency with which the above processes are carried out determines if a warehouse company can stand – out. These put a company on the market and help it in getting an edge over its rivals. Business increases and customer recommendations become appreciable. A well-established and organised warehousing structure is achieved only by these significant processes.
Related posts
- What Is Warehousing?
- What Is On-Demand Warehousing?
- How to start a warehouse business
- Everything You Need To Know About A Bonded Warehouse
- 8 Key Functions Of Warehouse Management System (WMS)
- 10 Practical Tips To Reduce Warehouse Costs
- 6 Major Benefits Of Bonded Warehouse
- 7 Best Warehouse Management Practices
- Logistics Warehouses Quickly Adopting Automation to Reduce Walk Time
- 11 Best Warehouse Management Systems (WMS)
- 6 Major Advantages of Cold Storage
- Industrial Shelving and Racking Vendor Diversification Required to Manage Supply Chain Disruption
- Top 11 Warehousing Companies In Hyderabad [2024 List]